Measurement
The Morehouse Proving Ring: A Century of Precision in Force Measurement
The ring had far-reaching consequences across multiple industries.
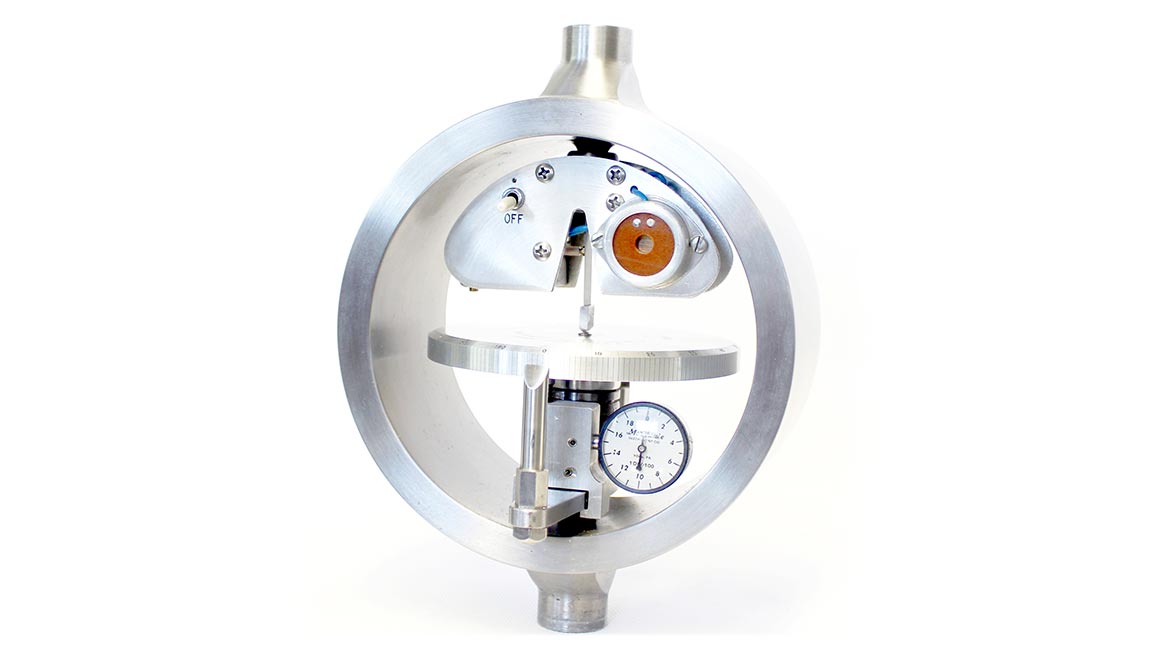
Image Source: Morehouse Instrument Company
As we celebrate 100 years of the Morehouse Proving Ring, it’s crucial to understand the historical context that led to its creation and its lasting impact on industry and safety standards. The late 19th and early 20th centuries were marked by rapid industrialization, bringing unprecedented technological advancements, and significant safety challenges.
In the 1920s, the problem of exploding boilers and steam engines became increasingly urgent as demand for power increased. When a boiler exploded, it effectively became a massive bomb, scattering debris over a wide area and often causing casualties. The maritime industry faced similar challenges, particularly with ship plates. These plates, typically riveted together, were subject to differential expansion and contraction rates, which could cause rivets to pop and compromise vessel integrity. Some historians even speculate that a fire aboard the Titanic, occurring just five days before its fateful encounter with an iceberg, may have weakened the ship’s structure, contributing to its eventual sinking.
At the heart of these industrial calamities lay a fundamental issue: inadequate material control and testing methods. The inconsistent verification of material strength and reliability in construction and manufacturing led to unpredictable performance under stress. Engineers and scientists of the time recognized that a material’s hardness was a critical factor in determining its suitability for various applications.
One method of testing material was a Brinell hardness test invented around 1900. This test involved pressing a 10 mm steel ball into the surface of the material being tested using a hydraulic cylinder. The size of the resulting indentation would then be measured to determine the material’s hardness. However, the Brinell tester had a significant flaw: the hydraulic cylinder generated a notoriously inaccurate testing force. This inconsistency in applied force led to unreliable and non-repeatable test results, making it difficult to establish consistent quality standards across industries.
S.N. Petrenko, an engineer at the National Bureau of Standards (NBS), started investigating these inconsistencies in the Brinell hardness testing machines. He identified inaccurate force measurements as the root cause of discrepancies in test results. Petrenko proposed using deadweights for more consistent force application, leading to the construction of a prototype deadweight machine at NBS.
Building on this success, Petrenko developed an improved machine with cast iron weights and enhanced loading techniques. To address the challenge of transferring laboratory accuracy to field testing, Petrenko conceived the idea of a metal ring that could measure deflection under load. H.L. Whittemore, head of the Engineering Mechanics Section, suggested incorporating a vibrating reed and micrometer screw, giving birth to the Whittemore-Petrenko Proving Ring.
The NBS workshops produced the first Proving Ring devices in the early 1920s, and they were looking for a company to collaborate with them in manufacturing the Proving Ring.
This is where Morehouse got involved. Morehouse was a local machine shop less than 100 miles from NBS headquarters. Morehouse had a skilled machinist named Harry Zumbrun, who was known as the person who could figure out how to machine almost anything.
Figure 1 Harry E Zumbrun and William S Morehouse. Image Source: Morehouse Instrument Company
Morehouse met with H. L. Whittemore and his wife at Morehouse’s home, May 30-31, 1925, to discuss the possibility of Morehouse manufacturing and refining the existing Proving Ring to sell. This meeting resulted in an agreement that Morehouse would begin manufacturing the Proving Ring. A sample Proving Ring and the blueprint drawing No. B 230 dated April 17, 1925, was sent to Morehouse. Upon receipt, Morehouse began manufacturing the Proving Ring. The first were made of 50-point carbon steel suggested by Whittemore, which was not a success. This was later changed to Carpenter 5/317 alloy steel.
The collaboration was nothing short of revolutionary. With the help of Dr. George K. Burgess, Director of the Bureau of Standards actively writing calibration laboratories interested in calibration work to purchase Proving Rings from Morehouse.
In 1925, Morehouse and the Bureau of Standards unveiled the Morehouse Proving Ring. The first of which manufactured by Morehouse was Serial Number 3, which was delivered on Oct 30th, 1925, to the Naval Aircraft Factory, Navy Yard, Philadelphia.
Figure 2 Morehouse Early Brinell Proving Ring S/N 14 Calibrated by U.S. Bureau of Standards test # 47197 May 24, 1926. Image Source: Morehouse Instrument Company
The Proving Ring was designed to calibrate Brinell hardness testers, addressing the critical issue of force inconsistency that had plagued earlier testing methods. By providing a means to measure and standardize the applied force accurately, the Proving Ring enabled more precise and reliable hardness testing across a wide range of materials.
Figure 3. Excerpt from Mr. Morehouse’s history of the Proving Ring notes. Image Source: Morehouse Instrument Company
The collaboration between Morehouse and NBS continued with Morehouse refining the Proving Ring to include integral internal bosses. The integral internal bosses were a significant improvement, addressing issues with repeated loading tests.
What was interesting about the NBS history is that the actual discussion above proceeded the application by NBS for a Patent.
Figure 4: Excerpt from Mr. Morehouse’s history of the Proving Ring notes indicating insufficient funds to patent some ideas first. Image Source: Morehouse Instrument Company
In one discussion, Morehouse admitted to not having enough money to patent this significant change in the design. However, refinement continued.
Figure 5: 100,000 lbf SN 45 with Integral Bosses May 23,1929. Image Source: Morehouse Instrument Company
The Morehouse Proving Ring consists of a carefully machined ring of high-quality steel, a precision micrometer, a dial, and a vibrating reed. When a force is applied to the ring, the ring deformation is measured using a reed with a contact point against a button mounted to a screw with a dial that is used to know the number of divisions at each given force point.
The key to the Proving Ring’s accuracy lies in its design and construction:
Material Selection: The ring is made from specially selected steel with consistent and well-understood properties.
Precise Machining: The ring is machined so the bending moment does not vary significantly in the region of the horizontal diameter, which leads to a nearly uniform strain distribution.
The Micrometer and Dial: The process of machining and lapping a screw in which the entire mechanism can accurately turn to provide a consistent reading.
Calibration: Each ring is individually calibrated against known standards, often deadweight standards, to ensure consistent and repeatable readings.
Figure 6: Jim Graham Calibrates an analog Morehouse Proving Ring using Deadweight Primary Standards. Image Source: Morehouse Instrument Company
The introduction of the Morehouse Proving Ring had far-reaching consequences across multiple industries. With the ability to accurately calibrate Brinell hardness testers, manufacturers could now reliably test and verify the properties of their materials. This led to more consistent quality control and the confidence to select appropriate materials for specific applications.
The more accurate material testing enabled by the Proving Ring, allowed for the development of more stringent safety standards. Industries such as shipbuilding, aerospace, and construction could now set and enforce higher standards for material strength and reliability. Perhaps the most significant impact of the Morehouse Proving Ring was the reduction in catastrophic failures of industrial equipment. By ensuring that materials used in boilers, steam engines, and other high-stress applications met rigorous standards, the frequency of explosions and structural failures decreased dramatically.
Figure 7: Morehouse Digital Proving Ring. Image Source: Morehouse Instrument Company
Over the past century, the basic principle of the Morehouse Proving Ring has remained largely unchanged, a testament to the soundness of its original design. However, advancements in materials science, electronics, and data processing have allowed for continual refinements and improvements. Modern Proving Rings often remove the screw and dial in favor of a linear gage and digital displays for easier and more precise readings.
The Morehouse Proving Ring is known for its stability, longevity, accuracy, and reliability. Proving rings, renowned for their exceptional stability and accuracy, have demonstrated remarkable longevity since their development in the 1920s, with some built in the 1930s still in active use today. This enduring reliability is attributed to their robust design and proper maintenance. These factors result in very little drift over extended periods, ensuring consistent and precise force measurements nearly a century after their initial fabrication. They often maintain uncertainties of 0.0125 - 0.025 % of full scale, making them incredibly precise instruments. Their reliability is so well-established that there’s even a Morehouse Proving Ring on the International Space Station.
Figure 8: A Morehouse Proving Ring being used on the International Space Station. Image Source: Morehouse Instrument Company
As we celebrate 100 years of the Morehouse Proving Ring, it’s worth reflecting on how this seemingly simple device has quietly underpinned much of the technological progress we’ve seen over the past century.
The legacy of the Morehouse Proving Ring is evident all around us - from the ships that cross our oceans, to the planes that fly overhead, from the buildings we live and work in, to the cars we drive. It ensures the safety and reliability of countless products and structures.
The story of the Morehouse Proving Ring is not just one of technical innovation but also of a commitment to safety and quality that spans generations. The company’s dedication to educating people about the importance of accurate measurements and their role in preventing disasters continues today. As we look to the future, with new materials and technologies constantly emerging, the principles embodied in this ingenious device remain as relevant as ever.
In celebrating 100 years of the Morehouse Proving Ring, we’re not just honoring a piece of engineering history but acknowledging a legacy of innovation that continues to shape our world. It’s a testament to the enduring power of human ingenuity and the profound impact that can come from solving seemingly simple problems with elegance and precision.
Looking for a reprint of this article?
From high-res PDFs to custom plaques, order your copy today!