Test & Inspection
The Right Hardness Testing Method for Your Metals Application
The right hardness test method depends on the material being tested and the specific requirements of the application. Understanding the differences among the available options helps determine which method will give you the best results.

EMCO-TEST DuraVision hardness tester, 0.3-3,000 kgf. Source: ZwickRoell
The most common methods used for testing the hardness of metals are Rockwell, Brinell, Vickers, and Knoop. Each of these methods employs different indenters and loads to measure the material’s resistance to plastic deformation.
Related Articles
Right off the bat, a key distinction between Rockwell testers and the Brinell, Vickers and Knoop testers is that the latter three use optical technology, while Rockwell does not—which generally makes it less costly, makes testing quick and easy, and the surface finish of the specimen is not critical. It is therefore, also the most commonly used method for metals testing on the U.S. market. The optical methods involve the use of a camera system, generally consisting of a digital camera, a light source, and lenses with various magnification strengths. Other factors to consider include:
Measurement Principle
Rockwell testers measure hardness based on the depth of penetration of an indenter into the surface of a material under a known load. Superficial Rockwell is used when the material being tested is relatively thin or has a surface layer that is significantly harder or softer than the bulk material. Brinell, Vickers and Knoop testers measure hardness based on the size and dimensions of the indentation created by a precisely shaped indenter and the load applied.
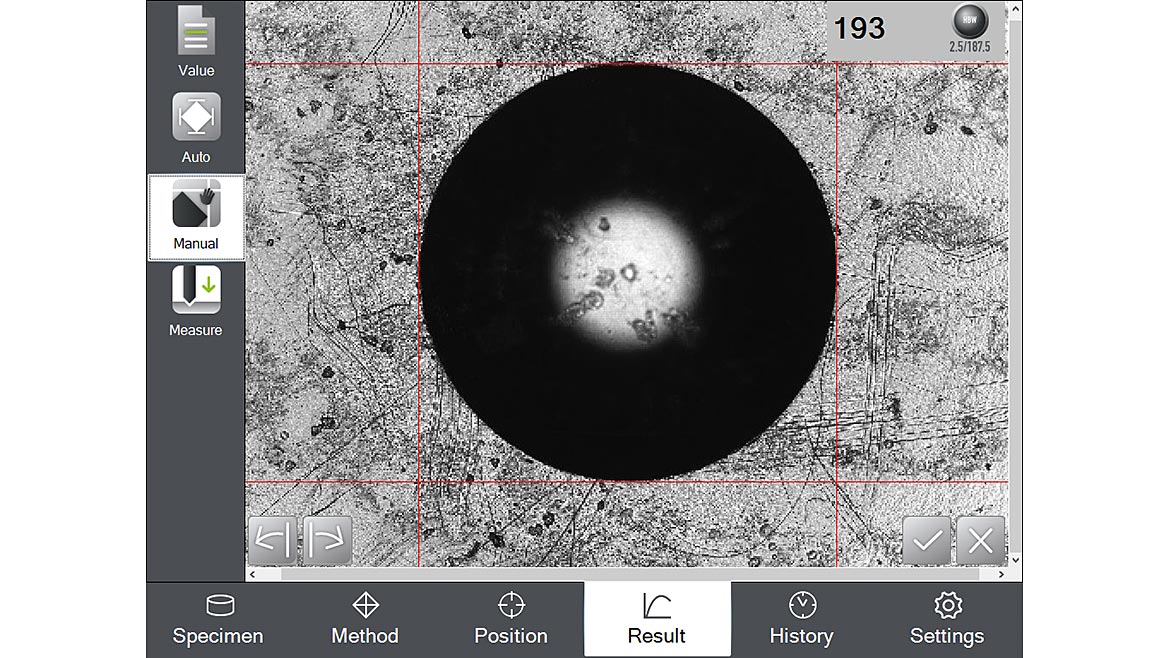
Indenter Geometry
The Rockwell method uses an indenter with either conical or spherical shape. Brinell hardness testing also uses a hard spherical indenter, but as already mentioned, rather than measuring depth, measures the diameter of the indentation. Vickers and Knoop hardness tests use a diamond-shaped or pyramidal indenter, where the diagonals of the indentation are measured, and the hardness value is calculated based on the applied load.
Material Types
Rockwell methods are well-suited for a wide range of materials, especially for metals and alloys—in many cases, the key consideration is the shape and surface of the sample to be tested. The information content gained also plays a role. Most often, a single measurement is carried out which provides general hardness information on the material or area being tested. Rockwell is often used for steel, aluminum, any other metals, plastics, or ceramics.
The Rockwell method is further categorized into various scales. Commonly used scales are:
- Rockwell C - typically used on materials with high hardness values, such as tool steels, castings and heat-treated materials.
- Rockwell B - comes into play for softer material, including non-ferrous metals like aluminum, copper alloys, brass and softer steel.
- Rockwell A - used on thin, hardened surface layers and shallow case-hardened parts. It is suitable for testing more delicate materials because it uses a smaller force compared to other Rockwell scales.
- Rockwell T - one of the superficial Rockwell methods and used for thin materials or surface layers, including steel sheets, coatings and plating. The test forces are even lower than with Rockwell A.
Brinell is mostly used for slightly softer metals, but also for large or rough surfaces (when high test forces are used), coarse-grained material, and/or high loads up to 3000 kg. It is commonly applied for tests on materials with a relatively low hardness range, such as non-ferrous metals, castings, and softer steels. Materials that fall into a very high hardness scale or thin and small components tend to be better suited for Knoop or Vickers testing.
Vickers methods are widely used for microhardness testing, which is essential for measuring the hardness of small or thin materials or for analyzing the hardness of specific microstructures in a material. This makes it valuable for examining thin films, coatings, and small features in various industries. Vickers is also often used for series measurements or mappings. This also includes CHD (case hardness depth), SHD (surface hardness depth) and NHD (nitriding hardness depth).
Knoop hardness testing is used primarily when the material being tested is thin, small, or has anisotropic properties. It is especially suitable when measuring the hardness of brittle materials such as ceramics, very thin coatings and individual microscopic features. It is used on composite materials, where it allows for targeted hardness assessments on individual constituents within the material. Knoop hardness testing is often used in R&D applications for materials characterization, failure analysis, and mechanical property investigations. It provides valuable insights into the microstructural properties and mechanical behavior of materials.
Load Application
The load selection depends on the material being tested, the desired indentation size, and the specific requirements of the application.
In general, the recommendation is to choose the highest possible load. This minimizes the influence of the surface treatment on mounted, cut or ground specimens. Also, with a higher load, the metallographic structure becomes more irrelevant. For specific materials or applications, there may be standard recommendations or specifications that suggest suitable loads. Industry standards or material-specific guidelines can provide valuable information on load selection.
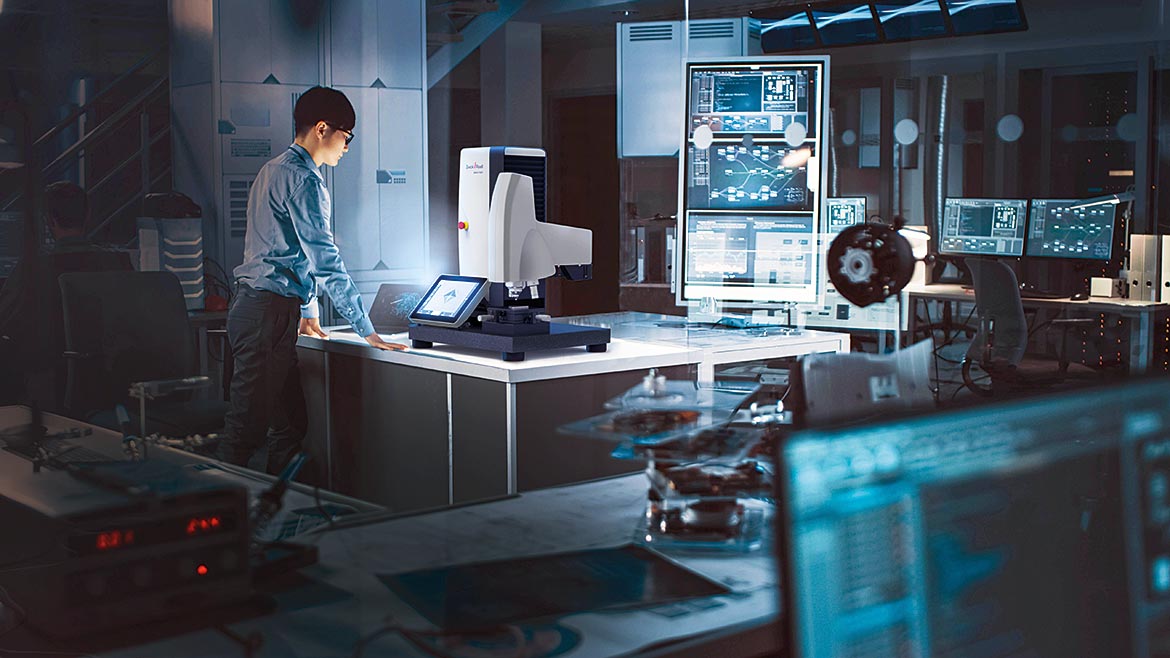
Micro vs. Macro Hardness Tester
Another common distinction is made between micro and macro hardness testing. Here, a basic differentiator is the application of lower loads and higher loads for different methods.
Micro hardness testing involves applying a lower test load, typically ranging from a few grams to a few kilograms, while macro hardness testers use heavier loads ranging from kilograms to tons. Micro hardness testing uses high magnification to accurately measure the dimensions of the small indentation. The test indentation is examined and measured using a microscope or an optical system. In macro hardness testing, the indentation is typically observed and measured without the need for high magnification.
Micro hardness testing is commonly used for examining small or thin samples, coatings, CHD Rows, NHD Rows, SHD Rows, hardness mappings or localized areas of interest. It is widely employed in materials science, metallurgy, and research applications to study microstructures, phase transformations, and hardness variations within a material. Macro hardness testing, on the other hand, is suitable for larger samples and provides a more general measurement of hardness for quality control purposes, material selection, or assessing bulk properties.
Looking for a reprint of this article?
From high-res PDFs to custom plaques, order your copy today!