NDT | Standards
Beyond Compliance: The Importance of Standards in the Mobility Industry
The key challenge lies in ensuring that these standards remain relevant, effective, and harmonized across global supply chains.
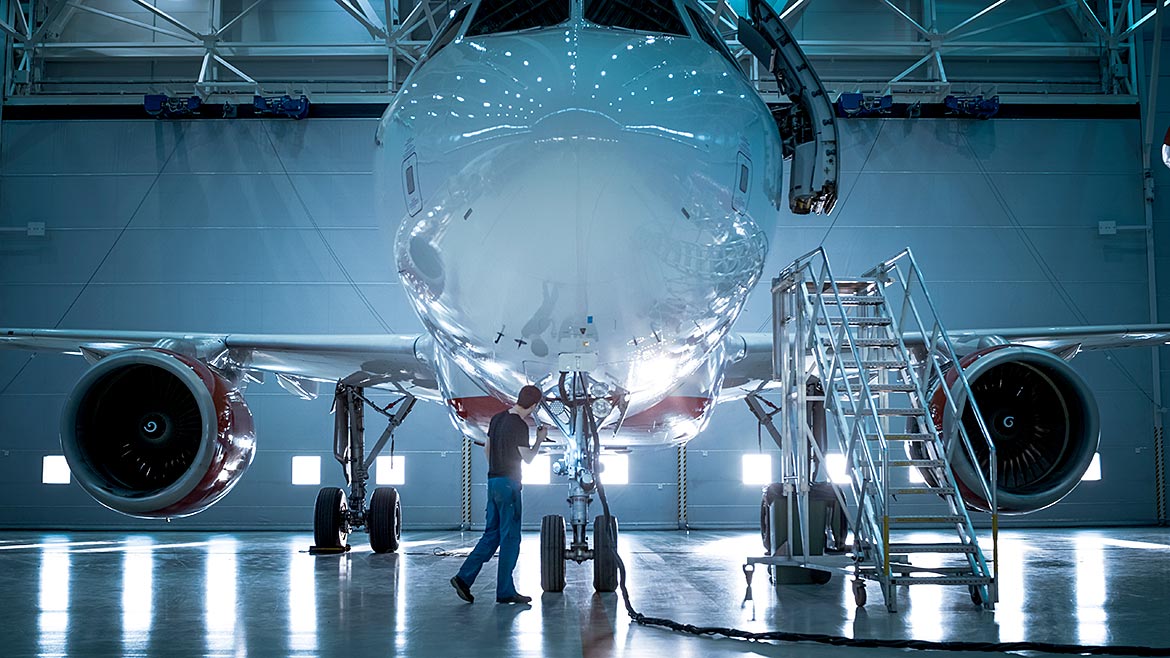
Image Source: gorodenkoff / iStock / Getty Images Plus
The relentless pursuit of quality is the engine driving progress in the automotive and aerospace industries. Quality is the bedrock upon which customer satisfaction, operational efficiency, and, most importantly, safety is built.
Maintaining standards of quality can foster continual improvement, preclude defects, and reduce variation and waste across supply chains. The pursuit of quality can culminate in flawlessly realized products that adhere to exact specifications.
In the automotive and aerospace industries, quality transcends excellence, underpinning the safety of operators, passengers and everyone traversing highways and airways.
As technology advances, global competition increases, and new challenges arise, mobility standards must continuously evolve to ensure safety, profitability, and consumer satisfaction.
Continued, guaranteed quality
Continual improvement is the goal of any successful Quality Management System (QMS). As the name suggests, this is an ever-moving goalpost, thus necessitating an ongoing commitment. With a shared goal of continual improvement in mind, quality management systems may be incredibly broad or narrow in scope. Some are more generic, like the international standard for QMS (ISO 9001), which can be applied to any sector. ISO 9001 is a foundational standard that can be used in any industry to ensure safety, increase efficiency and enhance customer satisfaction. These aims are met through leadership engagement and risk-based thinking to ensure that employees across all levels play a proactive role in fostering a culture of continual improvement.
While both industries implement ISO 9001, the evolution of quality standards in the automotive and aerospace industries nonetheless followed distinct paths, shaped by each sector’s unique risk landscape and operational demands. In the automotive sector, the emphasis on efficiency in mass production has led to the integration of quality management principles directly into manufacturing processes. Conversely, in the aerospace industry, where the production rate is lower, meticulous inspection and adherence to stringent standards has become the norm. This divergence evolved organically, driven by necessity rather than a unified strategic plan.
Industry-specific standards like IATF 16949 (automotive) and AS9100 (aerospace) build on ISO 9001 to provide a more tailored approach to quality management, addressing the unique requirements of each sector. The key challenge lies in ensuring that these standards remain relevant, effective, and harmonized across global supply chains.
The automotive industry
With over 300 million vehicles traversing the roads of the U.S. and Canada, the automotive industry faces immense pressure to ensure the safety and reliability of its products. Due to the scale of the industry, comprehensive inspection of every unit is nigh impossible. To address this, the industry has adopted a preventative approach, using mistake proofing methodologies to minimize defects. A preventative strategy is designed to ensure that potential issues are addressed proactively, reducing the reliance on end-of-line inspections.
This preventative approach to standards is reflected by IATF 16949, the gold standard for quality management in the automotive sector. Developed by the International Automotive Task Force (IATF) along with national automotive trade organizations from the U.S., UK, France, Germany and Italy, the IATF 16949 is built on the foundation of ISO 9001, with the addition of common processes and customer specific requirements from across the automotive sector. The IATF is specifically tailored to suit the high-volume demands of the automotive industry, facilitating continual improvement, defect prevention and reduction of variation and waste in the supply chain. These standards are achieved through a ‘Plan-Do-Check-Act’ (PDCA) cycle, which ensures that manufacturers are continually monitoring their work and proactively looking for ways to improve effectiveness and spot potential defects. By integrating standards into the entire manufacturing process, IATF 16949 empowers employees from across the supply chain to maintain standards, reducing the need for burdensome inspections.
In 2022, IATF 16949 was enhanced to help automotive companies better address the growing threat of breaches in automotive cybersecurity. IATF certification now stipulates regularly scheduled penetration tests to strengthen automotive cybersecurity. As modern vehicles have become increasingly interconnected, with digital systems controlling everything from parking sensors to advanced driver assistance systems (ADAS), automotive cybersecurity has become an increased concern among customers and manufacturers alike. Vehicle identification numbers (VIN) can be exploited to start and stop engines, remotely lock and unlock vehicles, retrieve precise locations of certain models, and even change car ownership. It is estimated that cyberattacks cost the automotive industry $22.5 billion, with industry experts forecasting this figure to grow, as AI integration is likely to introduce a whole new set of cybersecurity risks.
While the developments in IATF 16949 have gone some way to address cybersecurity threats, a new joint ISO/SAE standard, 21434, is the first standard specifically designed to protect automotive cybersecurity. Designed in alignment with emerging cyber security regulation from the UN Economic Commission for Europe (UNECE), the standard includes a new classification scheme, cybersecurity assurance level (CAL), intended to help in validating the process rigor needed for mitigating different threat scenarios. As vehicles become more deeply interconnected, we must ensure that, across the supply chain, employees are able to apply the same ‘Plan-Do-Check-Act’ mechanism when it comes to automotive cybersecurity.
The aerospace industry
The aerospace industry has significantly lower production volumes than the automotive industry but demands uncompromising quality, as the failure of a single component could have catastrophic consequences. Standards in the aerospace industry are therefore deeply rooted in rigorous inspection processes and a strong emphasis on proactively identifying and managing critical functional characteristics.
As such, in the aerospace industry we have seen the development of highly specialized standards, such as AS9100. Like the IATF 16949, AS9100 also builds on the foundation of the ISO 9001 but with added requirements related to safety, reliability, and regulatory compliance specific to the aerospace sector. What sets AS9100 apart from IATF16949 is the inspection processes embedded throughout the supply chain. AS9100 mandates First Article Inspection (FAI), requiring manufacturers to perform a first production run, which adheres exactly to the required production processes, documentation and tooling. Following this, a representative item from the production run is inspected to check that all requirements are met. FAI must be repeated any time a manufacturer makes changes that could invalidate the results. Through its rigor, AS9100 certification demonstrates a commitment to quality and provides a framework for continuous improvement. Though not mandated by law, it is often a prerequisite for doing business with major aerospace manufacturers and government agencies.
A new amendment to AS9100 was introduced in 2024 to recognize the importance of sustainability within aviation. Two new clauses stipulate that, alongside other relevant internal and external factors, organizations can consider climate change within their management system. While the revised AS9100 does not mandate any specific sustainability practices, the new clauses reflect that customer expectations and growing awareness of environmental and social issues are driving organizations to incorporate sustainability considerations into their AS9100-compliant quality management systems.
Alongside sustainability, the need to bolster supply-chain resilience is another urgent issue within the aerospace industry. Ensuring consistent quality across all tiers of suppliers has always presented a constant challenge due to the global and often complex nature of the aerospace supply chain. A study conducted by McKinsey found that supply-chain issues have become more prevalent in recent years, with aerospace executives 18 times more likely to report supply-chain-related issues, such as “shortages,” during earnings calls in 2022 compared to 2014. To address supply-chain challenges and maintain the required levels of quality, manufacturers are increasingly leveraging AI to analyze procurement information and proactively identify potential quality issues before they escalate. Standards have a role to play in fostering supply chain resilience by embracing new technologies like AI, IoT, sensors and advanced data analytics that would enable more manufacturers to shift their focus from reactive risk management to proactive, predictive analysis.
The future of mobility standards
In recent years, we have seen a notable convergence in automotive and aerospace standards. While aerospace retains its stringent focus on safety and reliability, the industry looking to ramp up production while managing costs is driving a gradual adoption of automotive-inspired methodologies and best practices, particularly in areas like lean manufacturing, statistical process control, and robust supply chain management. This convergence is not about diluting aerospace standards, but rather about strategically leveraging proven techniques from other industries to optimize processes, reduce waste, and ultimately deliver high-quality products more efficiently.
Moreover, with emerging challenges like cybersecurity, climate change and disruptions to supply-chains affecting both industries, the future is likely to hold further integration, with both sectors learning from each other to achieve operational excellence in an increasingly challenging global landscape. A 2026 update to ISO 9001 will likely reflect an increased focus on these emerging challenges.
Overall, the future of mobility hinges on our ability to strengthen and adapt quality standards to meet the challenges of a rapidly changing world. While standards like IATF 16949 and AS9100 provide a solid foundation, we must also address emerging challenges like cybersecurity and the urgent need to reduce our carbon footprint. Policymakers in the U.S. and Canada must prioritize the harmonization of standards and invest in research and development to ensure that our industries remain competitive, and our citizens remain safe.
Looking for a reprint of this article?
From high-res PDFs to custom plaques, order your copy today!