Management
The Enduring Importance Of Quality Standards
Some benefits of quality standards are obvious, while others don't get enough fanfare. The pandemic may have impacted how these standards are implemented.

Image Source: Drazen Zigic / iStock / Getty Images Plus via Getty Images
According to experts, the benefits of today’s quality standards are not well known.
Take ISO 9001, ISO 14000, and ISO 17021. These standards reinforce quality in any management system, says Steven Wilson, ASQE chair elect.
“ISO 9001 is all about quality management; ISO 14000 deals with the environment aspect of the business, and ISO 17021 tells the business what to expect to get certified in any standard,” Wilson says. “Even if these standards are not used to register or certify a business, they provide a strong operating foundation.”
Standards ultimately help to reduce variation, which increases predictable delivery and quality performance, says Bill Soller, principal, Corporate Advantage Network.
“An often-overlooked aspect of Dr. W. Edwards Deming’s teachings is that when you approach quality in a Deming way, you enjoy higher quality at a lower cost,” Soller says. “That is the ultimate equation: costs down, rework down, quality up, productivity up, and joy in work. Standards such as ISO 9001 get a company focused on developing a system to help control the quality of their processes.”
And yet, many leaders remain unaware of how fully implementing such standards can boost quality and lower cost.
“They only begrudgingly implement an ISO 9001 Quality Management System because a customer requires it,” Soller says.
Deming pointed out that people want to come to work to do a good job. He said it is management’s responsibility to support worker success.
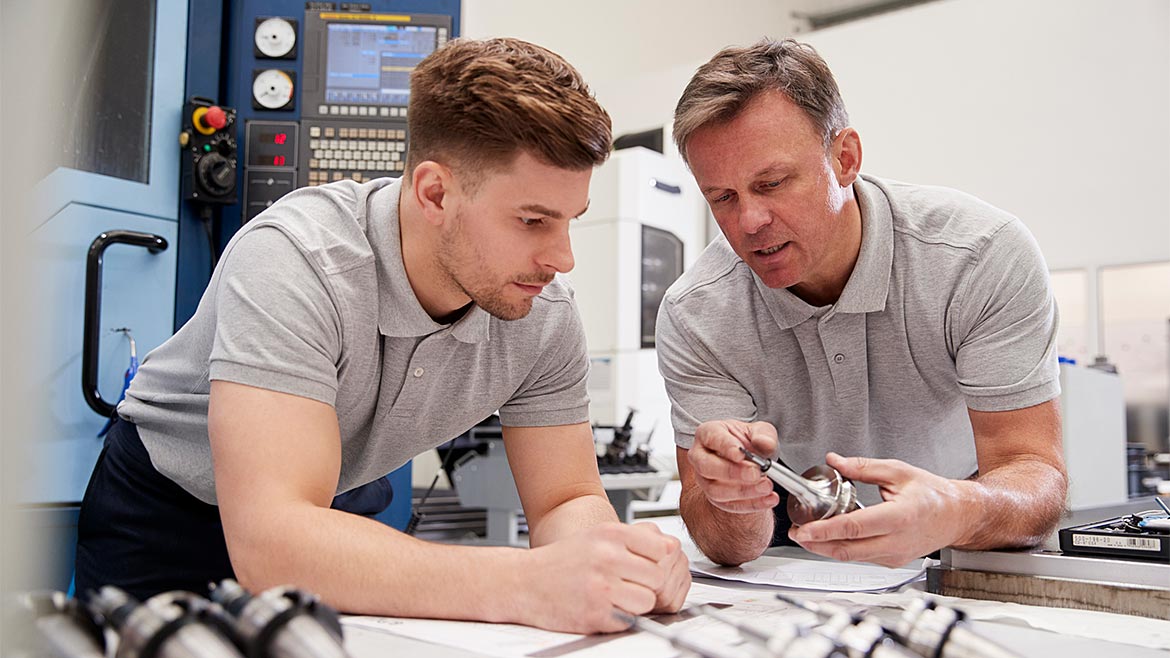
Image Source: monkeybusinessimages / iStock / Getty Images Plus via Getty Images
Companies that don’t have helpful certifications in place typically have only informal or undocumented processes, Soller adds. This makes implementing it muddy, which results inconsistent quality. Variation and costs spike as a result.
Standards are a strategic asset and should not be confused with regulations, experts say.
“Regulations tell all parties what must be. But standards tell us what should be,” Wilson explains. “Even as regulations change, which usually occurs with some sort of incident in our society, standards—especially quality standards—are modified as the parties grow and develop. They are always raising the bar.”
This helps manufacturers benchmark operations and remain competitive in their respective environments, he adds.
Accreditation is critical to ensuring that there is an effective quality management system that affords greater process control, reduces risk, and ultimately results in increased customer satisfaction and sustainability of our products and services, says Michael Byrnes, executive director, certification operations, ASQE.
To remain helpful, standards are regularly reviewed and updated.
“The foundations remain the same but changes in society and industry practices dictate a closer look at reasonable intervals,” Wilson says. “Otherwise, the standard not only becomes stale —it becomes obsolete.”
To prevent that, ISO standards are reviewed every five years, keeping them current and valid.
“About a decade ago, these standards were improved to follow the PDSA improvement cycle (Plan Do Study Act), which is often referred to as the Deming cycle (although Deming called it the Shewhart Cycle),” Soller says.
While this change does not make it more difficult to obtain certifications and credentials, it does give companies a means to demonstrate the reliability and consistency of outputs they produce.
“A further aspect of today’s standards is an alignment with one of Dr. Deming’s 14 points: Institute Training on the Job,” Soller adds. “The alignment exists because the certifications require work instructions and other visual aids to be a part of achieving repeatable quality in production processes and products and services.”
As an added benefit, written work instructions and visual aids drive down the costs of training and retraining workers even as the quality of the output increases.
“Keep in mind, Deming pointed out that people want to come to work to do a good job,” Soller adds. “He said it is management’s responsibility to make sure there is good training and good processes to support worker success and to continually achieve better outputs.”
The pandemic impacted standards, too.
For example, ASQ certifications moved to computer based testing with Prometric in 2016, says Michael Byrnes, executive director, certification operations, ASQE.
“As such, we were able to pivot all our certifications to Prometric’s new online Live Remote Proctoring (LRP) platform in a matter of weeks,” Byrnes says.
This enabled ASQ to continue to offer testing and to conduct it remotely.
“This pivot in testing modality to LRP further allowed ASQ to reach new business channels in over 50 new countries, where testing had not been possible due to a lack of physical testing facilities,” Byrnes adds. “In the end, the credentialing industry, which had largely resisted moving towards LRP for many years due in part to security concerns, had been positively disrupted by the pandemic.”
Although the pandemic didn’t change the standards themselves, it did change how they were implemented, reviewed, and audited against, experts say.
Virtual activities took center stage.
“In auditing terms: Working to utilize new tools and techniques to audit in a virtual world had to come,” Wilson says. “Many of us are still working through that process and it is clear that virtual activities are here to stay.”
The pandemic also affected the certification process, Soller says. For example, internal and external audits slowed at the pandemic’s onset. Some were even postponed for a few weeks. However, it didn’t take long for external audits to be conducted virtually, Soller says, “and so we caught up with demand quickly.”
The virtual approach lasted for about two years, Soller says.
Wilson, who works in food inspection as chief, Seafood Inspection Program, National Oceanic and Atmospheric Administration, says that the changing inspection process may even make standards more crucial.
“Imagine the inspection of a food processing facility against ISO 22000 (the food safety management family of standards) or even ISO 9001 and not being present at the facility,” he says. “The food must still be processed. The buyer must still have assurances that standards are met. Trade must continue. How do you use virtual auditing to meet these goals? I would say the standards became even more important in that all parties looked to the standards to see how to comply in this strenuous operating environment.”
Looking for a reprint of this article?
From high-res PDFs to custom plaques, order your copy today!