Management
The Death of Tactile Quality Control
The shift toward digital checklists and automated reporting has created an illusion of compliance.
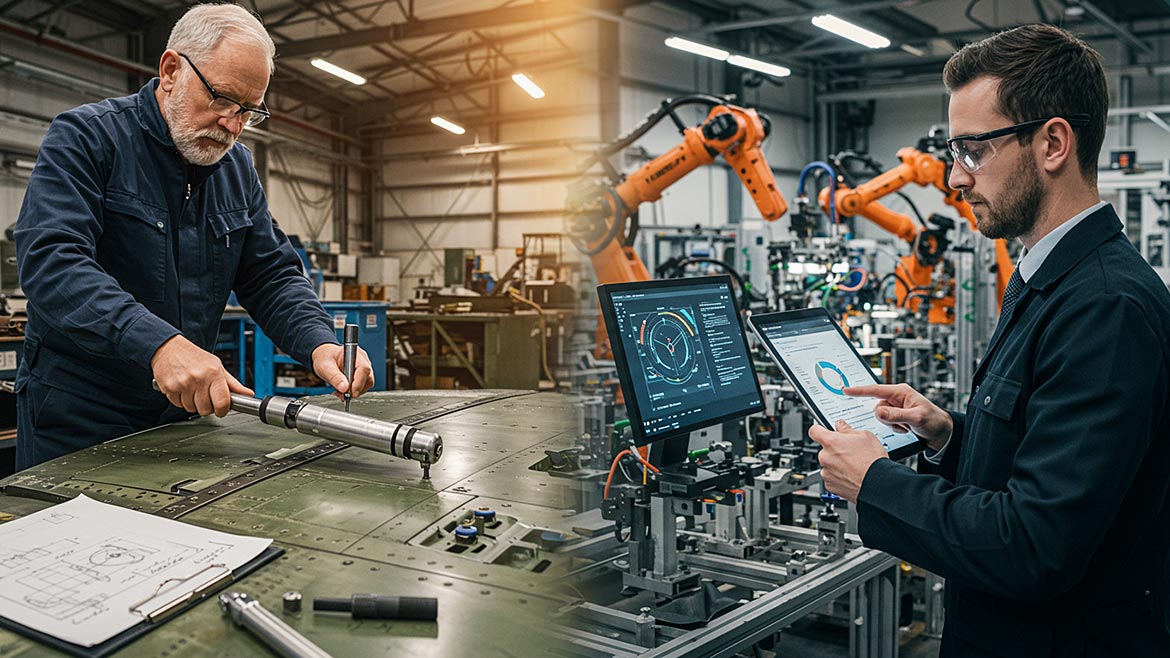
AI generated image showing old vs new quality assurance techniques. Source: ImageFx/Imagen3
Not long ago, quality assurance in aerospace was a narrow, hands-on process. Inspectors would physically verify installations: feeling the torque on bolts, tracing defects to their origin, and leaving behind ink-smudged paperwork as evidence of accountability. It was tactile, deliberate, and sometimes slower—but it worked.
Today, that same process has been digitized into checklists, creating a false sense of security. Instead of physically verifying that bolts are torqued to specification, an inspector might simply tap a box on an iPad, recording compliance without ever testing the hardware. Boeing’s D6-51991 digital product definition standard (AS9100D Section 8.5.2) may track every click, but as the January Alaska Airlines door blowout proved, even four missing bolts can slip through (LA Times, 2024). The computer log identifies the inspector by name, yet it doesn’t necessarily verify that the work was physically done, or even by that person. Aerospace standards demand traceability—each inspection must be clearly linked to the individual, with documented evidence of competence (AS9100D Sections 7.2 and 8.5.2).
The Disappearance of the Two-Man Rule
For decades, the two-man rule wasn’t just a procedural requirement—it was a psychological safeguard. In high-risk environments, such as submarine maintenance, two inspectors would physically verify every weld joint and assembly component. That redundancy not only reduced errors but also reinforced the inspector’s accountability.
Consider the Boeing incident: the missing bolts on a critical door panel were a glaring example of dual verification reduced to dual digital signoffs. If a second set of eyes had physically confirmed the fastener installation, the catastrophic door blowout might have been prevented. In safety-critical systems like an aircraft fuselage—which is as vital as a submarine hull—the probability of failure is too high to rely solely on a digital signature. When every approval becomes a checkbox, common sense is replaced by a performance that merely shows compliance, not proof of verification.
Inspector Training in the Tablet Age
The transformation of quality assurance isn’t limited to tools—it extends to the very training of inspectors. The American Society for Nondestructive Testing’s SNT-TC-1A mandates that personnel achieve a three-tier certification for visual and nondestructive inspections. Historically, inspectors were trained to see, touch, and evaluate components, ensuring that every surface finish and assembly met exacting standards before moving on to advanced tests like leak testing (LT), penetrant testing (PT), or ultrasonic testing (UT).
Today, however, many junior technicians are mastering camera angles for digital reports rather than the hands-on evaluation of physical tolerances. The USS Thresher disaster of 1963—a tragedy where rushed ultrasonic tests on silver-brazed joints led to catastrophic flooding—should have been a permanent lesson in the importance of tactile competency (Sullivan Testimony, 2003). Modern flaw detectors can auto-flag irregularities, but an over-reliance on pixels has created a generation that trusts digital readouts more than their own senses.
The Rise of the Paperwork Gatekeepers
Quality assurance was once free of bureaucratic interference. When I flagged a defect in a reactor valve back in 1965, I could take it directly to the Admiral’s office without intermediaries. Today, however, digital modules funnel every nonconformity through layers of middle management, turning defect reporting into a bureaucratic process. SharePoint portals and multiple digital signatures have replaced the direct, immediate reporting channels established after the USS Thresher was lost at sea.
The Thresher disaster prompted the U.S. Navy to establish the SubSafe Program, mandating that inspectors report defects directly to NAVSEA Code 08, bypassing the chain of command that might otherwise bury bad news. In modern aerospace, however, the question lingers: Who is the Boeing inspector reporting to? When every nonconformity must traverse layers of digital approvals, the courage to escalate a serious issue is often lost in the workflow.
Lessons from History: The USS Thresher and Beyond
On April 10, 1963, the USS Thresher (SSN-593) was lost during a deep test dive, claiming 129 lives. Investigations revealed that nearly 14% of its 3,000 silver-brazed piping joints were substandard. This failure in quality assurance underscored the necessity of direct, hands-on inspection and immediate defect reporting. The lessons learned from the Thresher disaster led to stricter protocols and the establishment of systems designed to ensure that no defect goes unreported.
Fast forward to today’s aerospace environment, and we see echoes of that same failure. The Boeing missing bolts incident is not merely a technological lapse - it is symptomatic of a broader cultural shift away from physical verification and towards digital compliance. The historical lesson is clear: when companies remove the human element from quality assurance, the consequences can be catastrophic.
Fixing the Future: A Hybrid Approach to Quality Assurance
We don’t need less technology; we need smarter integration of touch and tech. Hybrid solutions already exist to bridge the gap between digital efficiency and tactile reliability:
- Hexagon’s Nexus blends digital instructions with physical measurement tools, ensuring that automated processes are validated by direct, physical verification.
- GE Aerospace’s Catalyst program revives protocols reminiscent of the Thresher era, reinstating defect escalation paths that bypass middle management bottlenecks.
To safeguard against future failures, aerospace companies must reintroduce hands-on quality control. Inspectors need to be trained to trust their senses and document their findings both digitally and on paper. Organizations should enforce the two-man rule not as a digital formality but as a tangible process requiring independent physical confirmation of every critical installation.
Conclusion
The missing bolts on a Boeing aircraft door aren’t just a minor oversight; they are a wake-up call. The shift toward digital checklists and automated reporting has created an illusion of compliance, masking the critical loss of tactile quality assurance. We must re-establish a balance where technology enhances but does not replace human judgment. The future of aerospace safety depends on restoring true accountability, ensuring that every inspection is not just recorded, but truly verified—one bolt at a time.
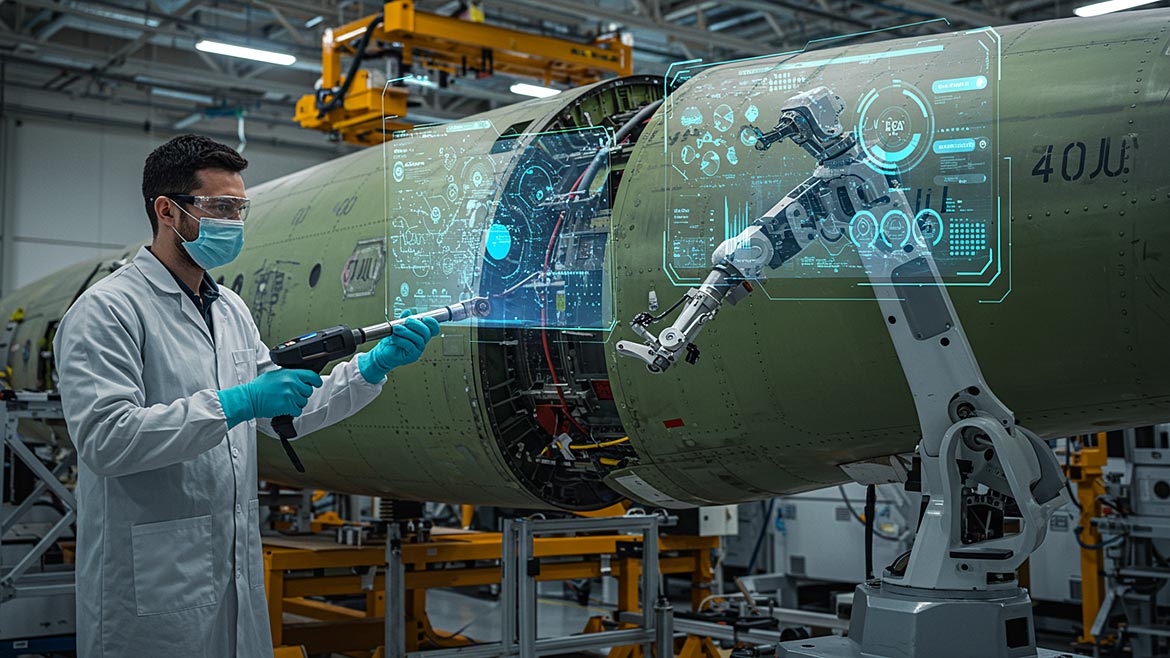
References
- AS9100D: Quality Management Systems – Requirements for Aviation, Space and Defense Organizations
- Boeing 737 MAX 9 Missing Bolts Incident(2024). Los Angeles Times. https://www.latimes.com/business/story/2024-02-06/boeing-737-max-9-ntsb-report
- Sullivan, P.E.(2003). Statement to House Science Committee on SUBSAFE Program. U.S. Navy.
- NAVSEA Instruction 4790.26A(2019). Naval Sea Systems Command.
- ASNT SNT-TC-1A(2023). Personnel Qualification and Certification in Nondestructive Testing.
Looking for a reprint of this article?
From high-res PDFs to custom plaques, order your copy today!