NDT | Ultrasonics
Thickness Gages in my Lifetime
Today’s ultrasonic thickness gages are more powerful and more versatile than at any other time in the history of NDT.
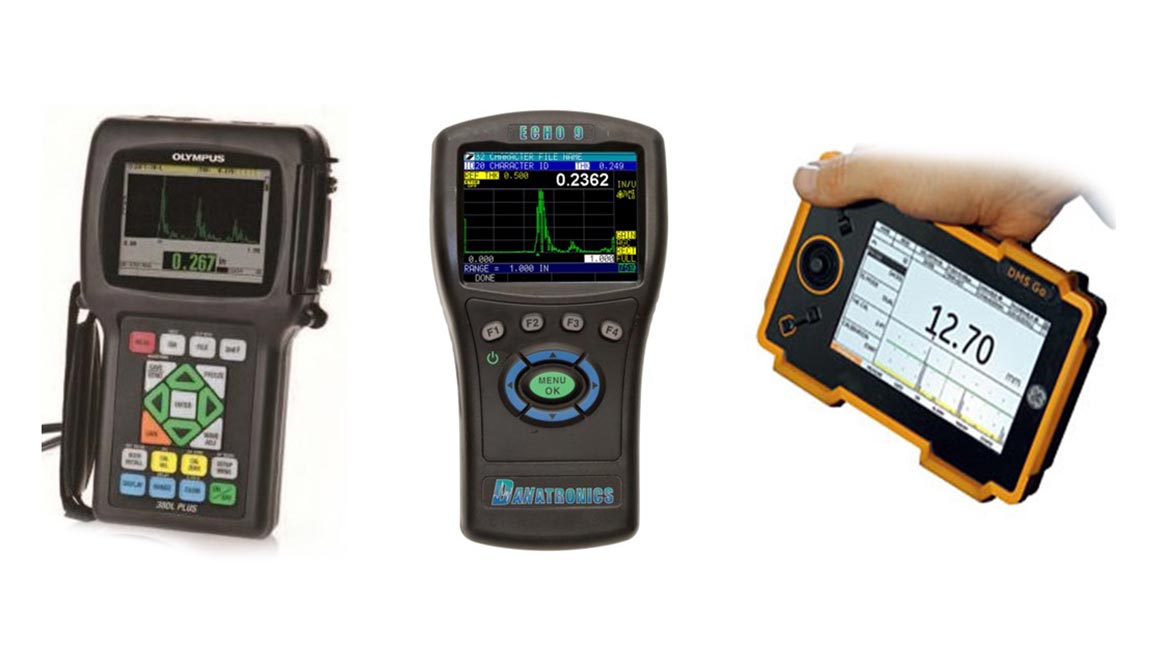
Image Source: Danatronics
Throughout my 40 years in nondestructive testing (NDT), thickness gages have gone through a tremendous journey. From analog to highly intelligent digital gages, the transformation has been amazing.
Ultrasonic thickness gages operate as a system consisting of a gage with a pulser/receiver, a transducer and cable. The transducer transforms electrical energy into mechanical energy, or vibrations. The time it takes these vibrations to enter a homogeneous material, reflect off an interface, and return to the transducer, at a given sound speed (velocity), is calculated as a thickness.
UT gages were used as a replacement of mechanical dial calipers and micrometers. The thickness gage was a one-sided measurement, capable of measuring very thin and very thick materials with the same gage. You need to calibrate the gage for the type of material being tested.
The first ultrasonic thickness gage I worked with was a completely analog gage that had a 4-digit readout and a 4-segment velocity reading that was adjusted by + and – pushbuttons for calibration. Although battery powered and portable, most applications were performed in a lab or bench testing, consisting of metals testing.
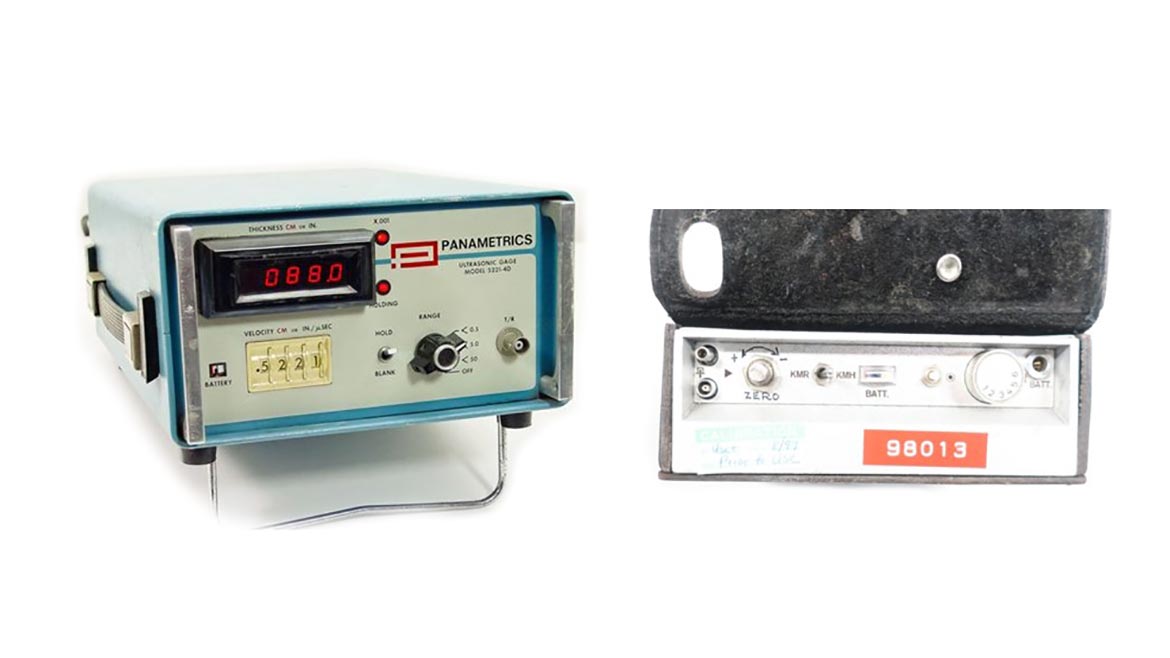
At that time, the only way to record readings was to write them down. From the customer’s view, there had to be a better way to document their readings. Ultrasonic manufacturers listened and a few years later, the first data-logger gages were born. With this change also came longer battery life and RS-232 for downloading their readings. Most gages had a 1,000 reading limit, with numeric identification. The first data-logger gage I was exposed to was a two-piece unit with the gage and separate datalogger. Although this was a major breakthrough, the two-piece design was not well received.
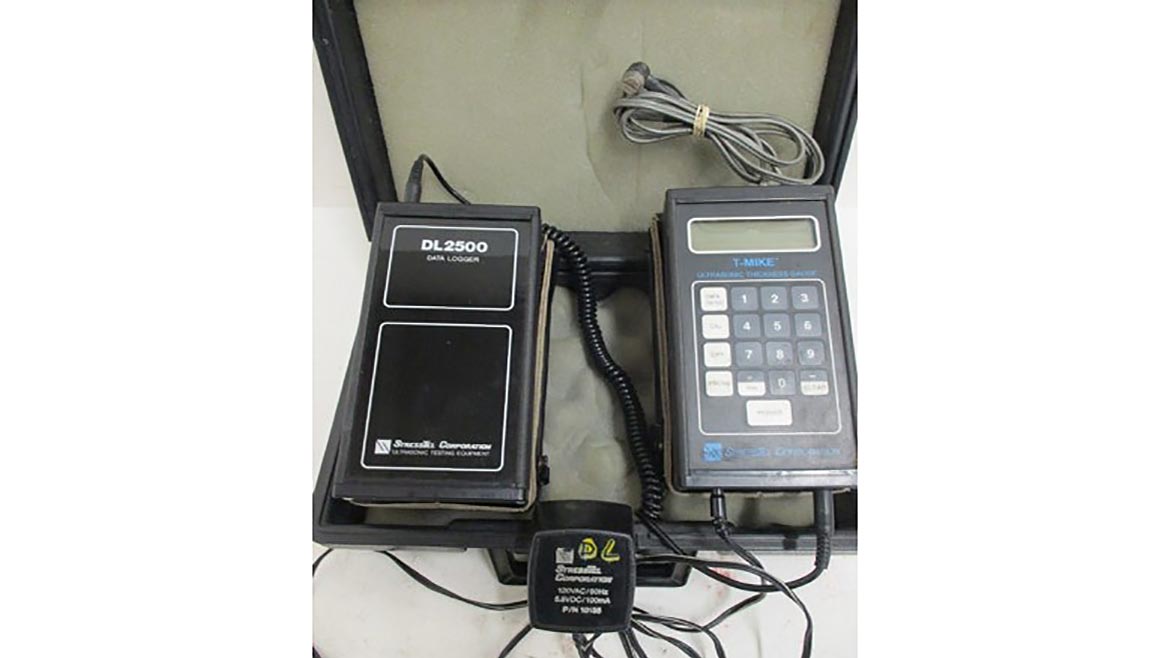
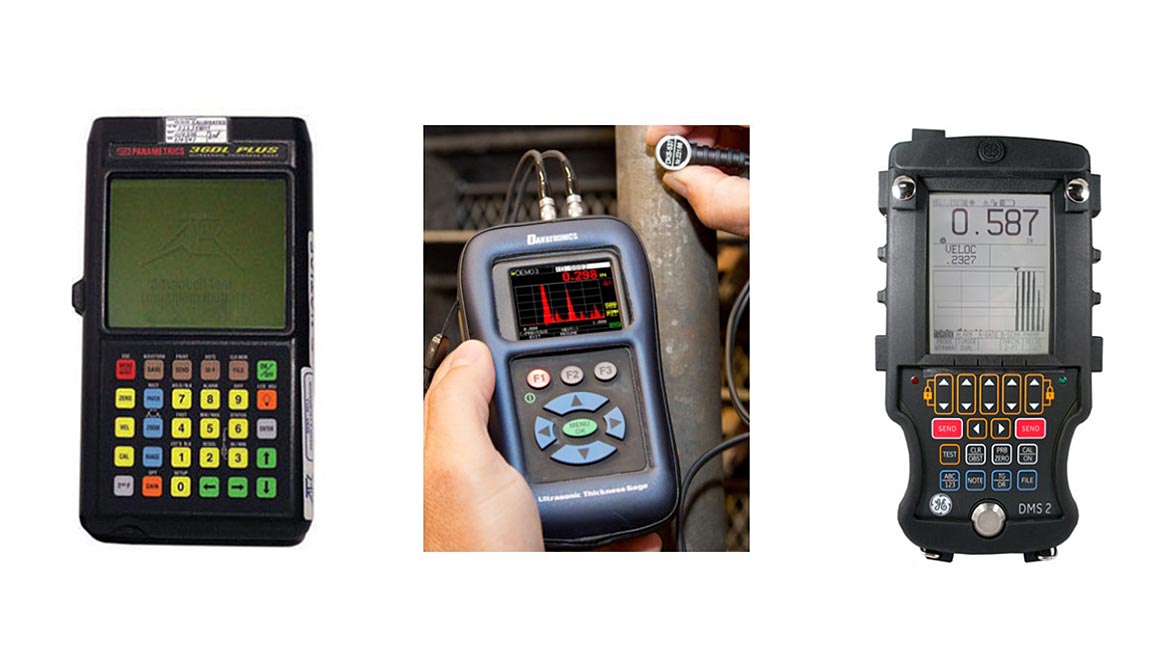
Industry then asked for another innovation after several near accidents at various plants. A waveform was needed to confirm that the corrosion thickness reading shown was correct. The problem was when a reading was taken outside the limitations of the dual transducer, unknown to the technician, the reading would double or sometimes triple the actual reading, thus making a very thin reading appear thicker and within tolerance. The waveform or A-scan helps a trained technician verify the reading is proper and true.
Before the A-scan thickness gage, the readings were taken with a very heavy and burdensome flaw detector. Although the waveform thickness gages were larger in size to incorporate the additional space for the A-scan and thickness reading displayed at the same time, they were still small and lighter weight by comparison. With datalogging capability, you were now able to store the thickness reading and A-scan in the gage for reporting later.
At the same time, precision thickness gages were having their own technological growth. Precision gages typically have a higher resolution, .0001”, and higher frequency transducers for testing very thin materials and difficult to penetrate samples. Transducers were single element contact, delay-line, or immersion. Datalogging was introduced, as was waveform verification.
As electronics and software technology was growing at a very fast pace, the corrosion thickness gage market also grew. Industry demanded more out of the gage manufacturers and they delivered. The gages had an immediate effect on the industry with added features such as a larger screen to incorporate the A-scan and thickness reading, Echo-to-Echo, B-scan, and greater battery life.
Increased datalogger capacity and alpha-numeric identifiers were added along with sequential, 2D, 3D and boiler layout formats. There were also alarms added to allow a high and low set point, the gage would beep if the reading went over or under the set points.
Some of the early features during this time were stored transducer setups, expanded datalogger storage, encoded B-scan, and fast mode. Additionally, coating measurements and substrate were added.
Gages today are feature rich, with color screens, and measurement features such as temperature compensation, which allows the gage to compensate a reading for an elevated temperature using an algorithm to recalculate the reading that was taken on a material that is at a much higher temperature than the ambient temperature the gage was calibrated. Alarms that excite three of your five senses; hear a beep, see a color change, and feel the gage vibrate. Oxide scale measurement on boiler tubes can be measured using high frequency delay-line transducers. Phase reversal detection senses the change in the RF waveform, due to a delamination or other acoustic anomaly.
With Industry 4.0, many manufacturers have added wireless technology to their gages, such as Bluetooth and WIFI for sending data to the Cloud, Android and iOS devices. This helps to speed up the reporting process. You are also able to see live data from the gage on one of the Bluetooth devices, via an app, to help verify a difficult call. This advancement also allows data to be interfaced to an IDMS, Integrated Database Management System.
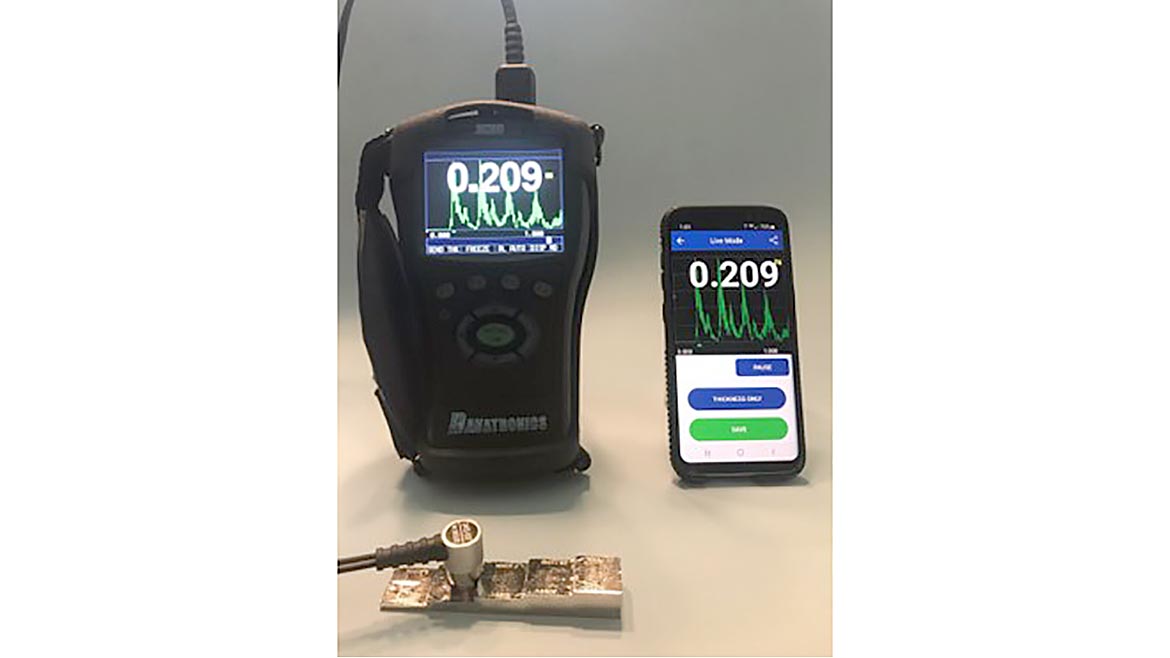
Even the ability to use software to add more capability to your thickness gage, such as precision thickness or even flaw detection, has made these handheld gages performance savvy.
Today’s ultrasonic thickness gages are more powerful and more versatile than at any other time in the history of NDT. They are used more than any other ultrasonic instrument, and will continue as the workhorse in the industrial market. Based on the current needs from the field and the speed at which electronics and software are changing, the future of the ultrasonic thickness gage is looking very good.
Looking for a reprint of this article?
From high-res PDFs to custom plaques, order your copy today!