Measurement
Multisensor Metrology Explained
Your multisensor metrology questions answered.
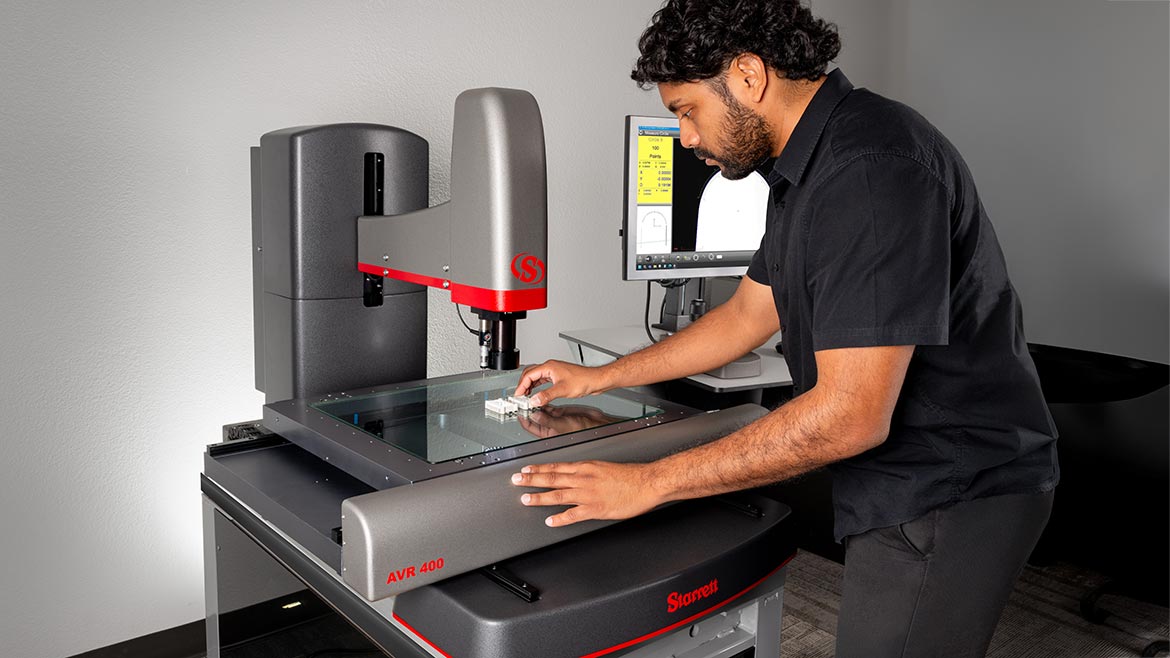
Starrett AVR400 Multisensor Vision System featuring a touch probe utilized for quick acquisition of discrete points along a part’s profile as well as Z-axis measurements. Image Source: Starrett
What is multisensor metrology technology? Multisensor metrology combines numerous methods and capabilities to analyze and quantify part measurements using repeatable and reproducible techniques. Providing access to digital camera measurements, touch probing and digital overlays all in one system are typical examples of multisensor metrology.
Multisensor systems offer exceptional speed and efficiency, while maintaining accuracy. For example, dual optical systems may work in tandem for measuring a diverse range of features with one single device. A primary zoom lens enables small intricate features to be inspected with high precision and resolution of up to 2 microns. A secondary large field-of-view camera is equipped with a telecentric lens that can simultaneously inspect large areas of a part, or an entire part itself.
A broad range of zoom options also means that measurement configurations can be custom tailored to meet the specific application requirements for each user. This advancement in measurement technology allows companies to have the best of both worlds in one metrology system, without the need to change lenses or re-calibrate the unit. Dual optical systems, as well as touch probe capability, allows users to inspect a part with a wide variety of geometries and feature sizes.
With increasingly complex parts being manufactured with advanced multi-axis machine tools, a multisensor metrology system provides the necessary functionality to verify the conformance of parts with zero defects. Having a validation process in place ensures that you’re prepared for the next job that comes down the line.
Why is multisensor metrology technology so important for today’s manufacturers and quality labs?
In today’s fast paced manufacturing environment, multisensor metrology systems give operators and quality personnel the tools to verify conformity using an automated approach, freeing up time so they can focus on other operations. Since finding and retaining knowledgeable and skilled employees is on on-going challenge, providing easy-to-use metrology solutions is of utmost importance.
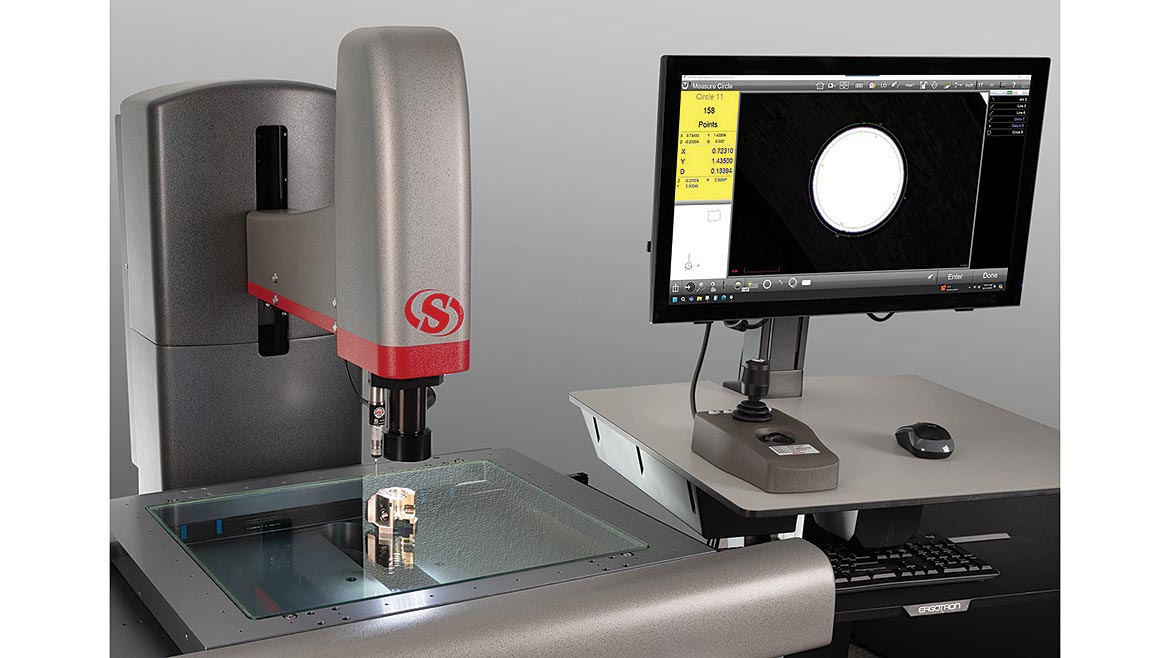
Multisensor systems should be equipped with user interfaces that make the system’s capabilities approachable and easy-to-use. One of the top benefits of modern metrology software programs is the speed of throughput due to features such as automatic part recognition. Users can create a part measurement program that comprises the desired features of a part for inspection, which can automatically be saved in the system or to a network.
Automatic pattern recognition can be extremely productive, especially for a high volume, low mix of parts. Pattern recognition is where inspection routines are created for workpieces based upon the master template, complete with tolerances. Precise stage motion and lighting control can be built-in as programmable steps to ensure maximum repeatability, regardless of operator skill. Once the program is created, an operator can place a sample on the stage and initiate the routine. When the routine is initiated, the system will automatically run the inspection, taking all relevant data points and providing accurate results in seconds.
Programmable light output options can also be built into the program as defined steps, including being called up as the part recognition program initiates. Once the program is created, placing that part within the camera’s field-of-view allows for the saved program to initiate and run the inspection. This enables fast, accurate and repeatable results. Features such as a “Superimage” function allow a user to piece together multiple camera frames in order to view a large part in one single image. Optional touch probe capability is now better than ever, providing quick acquisition of discrete points along a part’s profile. Touch probe supporting 3-D geometry mapping has been improved and advanced as well.
These advancements, when combined with CNC control, edge detection, and one touch measurement facilitate what is known as “walk-up metrology.” Walk-up metrology enables multiple operators, including those right on the shop floor, to utilize the same system for a variety of applications. This versatility and ease of use significantly helps with bottlenecks in the inspection process and dramatically increases speed and workflow efficiency.
Are manufacturers hesitant to adopt multi-sensor technology, and if yes, why?
The biggest hurdle to adopting multi sensor technology is typically the fear of training operators to use the equipment. However, multisensor technology available today has come a long way to address user friendliness to assuage those fears.
Can some comparators be considered multisensor?
Optical comparators have been a crucial, reliable and successful technology for the past 100 years, and offer versatility and durability on manufacturing floors. Comparators have multisensor capabilities ranging from digital mylar overlays for checking profiles, to optical edge detection which takes operator subjectivity out of the equation.
How does one determine what solution is best for the application at hand?
Selecting the right multisensor system for your application will provide advanced capabilities and flexibility for efficient, accurate quality control.
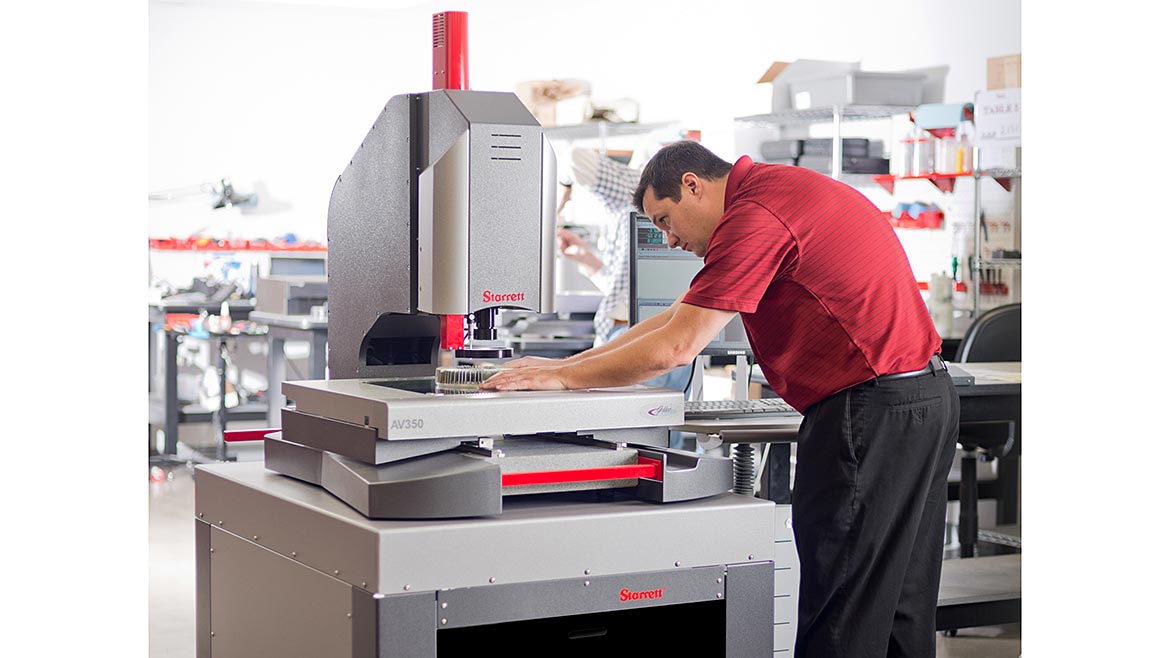
Here is a checklist that may help you begin the selection process:
- Measurement complexity. A 2D optical comparator may suffice for simple measurements and visual comparison, but more complex medical and aerospace parts, for example, may require a multi-sensor metrology system with CMM-style touch-probe capability.
- Measurement throughput. A manual system may be an option for prototypes, occasional or short run measurements by the QC department, but an automatic CNC system is a more economical solution if complete production runs are to be verified.
- Tolerance requirements. A vision metrology system with a granite base may be required for meeting tight tolerances, crucial for manufacturing medical parts. Tight tolerance may also indicate the need for higher magnification optics.
- Size and weight of parts. A benchtop optical comparator or video metrology system may be appropriate for small parts, while a larger, floor-standing system can be helpful for large and/or heavy parts.
- Interface. Various interface options are now available for both optical comparators and video-based measurement systems including digital readouts, touch-screen PC solutions and rack-mounted computers with monitors/ software.
- Software features. Capabilities can range from a simple two-axis readout to 3D multi-sensor capability with a rich set of measurement software tools, CNC control, statistical packages, DXF CAD file import and export, touch-screen operation with Windows Operating Systems, and network connectivity.
What skills are needed for getting up to speed using multi-sensor technology? Is training required for implementation and how long does that take?
Powerful and intuitive software has drastically reduced training requirements from weeks or months to days. New operators can expect to be using a multisensor system on day one of training.
What questions about multisensor systems are you getting most commonly from your prospects and customers?
We are often asked about the software maintenance agreements. The agreements can pose a cost that sometimes can rival the cost of the machines themselves. However, some do not have a software maintenance cost, freeing up the budget for other process improvements.
Would you give an example or two where multi-sensor technology improved productivity versus an older (non-multi-sensor) method?
Often, we have seen our multisensor systems implemented to replace hard gaging and manual measurements where data is either not being captured or written down, or is written down with errors. For example, aerospace and defense contractors need to capture data for traceability and making critical product improvements for consistently producing accurate products. A multisensor system with automated software capabilities captures data automatically for analysis and exporting, eliminating any manual errors and saving time.
Looking for a reprint of this article?
From high-res PDFs to custom plaques, order your copy today!