Column | Fellow Traveler
Supply Chains: Five-Fold Reconciliations
The Quality function should have a meaningful role in the qualification and selection of vendors.

Image Source: pigphoto / iStock / Getty Images Plus
The purpose of this article is to show how a robust supply chain should be successfully reconciled across five sources of information: Approved Vendors, Master Agreements, Transactions, Deliveries, and Payments.
The success or failure of an organization’s supply chain is evaluated not only by overall costs and savings, but its internal alignment and adherence to protocols, agreements, contracts, and delivery commitments. Without internal consistency, the variations will lead to various risks and issues including missed opportunities for discounts and negotiated terms, redundant orders creating excess inventory, delayed deliveries and payments, and imbalanced accounts.
In this narrative, some recognizable comparisons will be profiled, based on actual experience. This was largely reflective of a previous effort to migrate these operations into a common information technology platform. Enterprise Resource Planning (ERP) can be applied to large-scale and nimble businesses by following a common framework.
1. Approved Vendors
The Quality function should have a meaningful role in the qualification and selection of vendors. This extends beyond the ability to reliably deliver the required products and services. In the current geopolitical environment with global conflicts and multinational entities, the very eligibility of a vendor may be affected by prevailing trade restrictions or controversial strategic affiliates.
The supply chain is a function of trust. Those vendors deemed to be critical to the success of an organization and its deliverables should be provided with more extensive opportunities to integrate their methods and practices to align with those of their customers. This is regularly demonstrated by Tier 1 suppliers to major manufacturing companies.
The status of Approved Vendors should be time-bound and revisited for renewal or revision periodically, when there are significant ownership or governance changes to the affected organizations (i.e. acquisition by another company), or in response to a persistent series of significant quality issues. These details should be updated and reflected within the organization’s information technology system (i.e. ERP, MRP).
2. Master Agreements
In this context, the Master Agreement is a broad term that characterizes the globally accepted terms and conditions of how business is performed between the vendor and the purchasing organization. If the prerequisite of a Master Agreement is Approved Vendor status, those approval terms can be applied toward the trust and familiarity between the organizations.
For the scope of this article, some examples of a Master Agreement can incorporate global agreements for expectations of required quality, discounts and payment terms, processes for change orders, and escalations of claims for quality issues. For this reason, the foundational agreements from the Approved Vendor process should be aligned with the specific agreements made for products and services.
The status of Master Agreements should be time-bound and revisited for renewal or revision periodically, when there are significant ownership or governance changes to the affected organizations (i.e. acquisition by another company), changes to the status of Vendor Approval, or in response to a persistent series of significant quality issues. These details should be updated and reflected within the organization’s information technology system (i.e. ERP, MRP).
3. Transactions
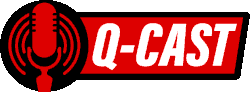
Overcoming Threats to Quality Culture
Daniel Zrymiak profiles some recognizable threats to quality culture, based on actual experience. The quality function of an organization must constantly monitor the operations and discussions for the evident presence of these and other threats to success, and be prepared to take appropriate and commensurate actions.
Watch the video of this podcast here.
Listen to more Quality podcasts.
The nature of such transactions should range from small purchases to extended programs for the delivery of a series of products and services. The prevailing documents could be Purchase Orders, Statements of Work, or Proposals, all of which should be uploaded to the organization’s information technology ERP/ MRP system. It is important to ensure that pricing, terms, and conditions for transactions are aligned with those negotiated as part of a Master Agreement with an Approved Vendor. This is often overlooked when a local sales representative from the vendor quotes a price with a higher margin than the previously negotiated but disregarded global Master Agreement (often with volume discounts).
The transactions may encounter quality issues with the products or services provided. The resolutions and corrective actions for such events should not emerge on a random, ad hoc basis, but should also follow and be aligned with the foundational agreements already established and documented during the Approve Vendor and Master Agreement processes. The transactions then become repeatable demonstrations of those earlier agreements.
In the event that transactions encounter issues not previously defined by earlier agreements, this could be the basis for modification. For example, if a printed circuit board malfunctioned when exposed to -40C weather conditions, the resolution of this performance gap may not have been previously addressed within the Master Agreement. If the current vendor could not meet this requirement, a new Approved Vendor would be sought for products that could withstand these temperature conditions.
The status of Transactions is time bound and should be updated to reflect the progression through the stages of purchase, development, and readiness for delivery. Also, any changes or cancellations to current agreements with Approved Vendors or Master Agreements should be propagated to ensure that Transactions are updated accordingly and cancelled if necessary. These details should be updated and reflected within the organizations information technology system (i.e. ERP, MRP).
4. Deliveries
The term Deliveries is intentionally broad and is meant to represent and reflect the fulfilment of the product or service. For physical products, it could simply be the provision of the finished product to the warehouse. When this is a service or modified product, the steps to completion are more complex.
The Quality leader has many intermediaries between the vendor and the end result: contractors, systems integrators, site leadership, technical advisors, and the layers of regulatory control including international customs agents. These and other third parties may be sought to provide their approval and consent for the delivery and acceptance of the products and services.
In product development the term Definition of Done informs the organization of the acceptance criteria which must be reached. This should be reconciled back to the Purchase Order, Statement of Work, or Proposals, which should be reflected within the Acceptance Criteria of the work performed. Without this reconciliation, there are risks that expected features and deliverables will be overlooked. Alternatively, if the organization “over-delivers”, they will not recover the costs of design and development which resulted in the excessive solution. (i.e. “gold-plating” the product).
The status of Deliveries is time bound and should be updated to reflect the progression through the applicable stages of ordering, shipment, design, development, inspection, verification, validation, third party approvals, and commissioning. These details should be updated and reflected within the organization’s information technology system (i.e. ERP, MRP).
5. Payments
The term Payments represents the financial or exchange made to complete the terms of the transaction. This may be monetary or some other value of exchange. When the transaction is fulfilled, there should also be a reconciliation relative to the explicit terms from Approved Vendor and Master Agreements to ensure there are no gaps nor missing items.
For example, if the Master Agreement specifies that payment is expected 30 days after delivery, these terms should be equally represented on the Purchase Order or Statement of Work and the corresponding Invoices. Payment terms for shipping and customs clearance are also important to clarify so that these transactions can be smoothly and consistently prepared and performed without delays.
The financial aspects of supply chain management are easier to control if there are ample and consistent references within the internal information technology system (i.e. ERP/ MRP). In contrast, if these references are inconsistent, obsolete, or outdated, these gaps must be resolved for current and future transactions and payments.
The status of Payments is time bound and should be updated to reflect the progression through the applicable stages of invoicing, collection, receipt, and balancing. These details should be updated and reflected within the organization’s information technology system (i.e. ERP, MRP). Without the five-fold reconciliation, payment could be delayed due to inaccuracies from the Approved Vendor, Master Agreement, Transaction details, or Delivery outcomes.
To summarize, a Quality leader should support the five-fold reconciliation framework to properly establish, monitor, and govern the supply chain. This is most effectively administered using an integrated information system which captures the necessary details at all stages and levels. While access to some information should remain privileged and restricted, the key working details should be readily provided for quick and correct alignment.
Looking for a reprint of this article?
From high-res PDFs to custom plaques, order your copy today!