Automotive
The Impact of Electric Vehicles on Automotive Manufacturing: The Role of First-Time Quality, Digital Twins, and Dimensional Engineering
Unlike internal combustion engine vehicles, EVs rely on complex battery systems, electric powertrains, and sophisticated software that must work seamlessly together.

Image Source: PhonlamaiPhoto / iStock / Getty Images
As electric vehicles (EVs) continue to revolutionize the automotive industry, the pressure on manufacturers to refine their processes and achieve first-time quality has never been greater. The rapid adoption of EVs, driven by consumer demand for more sustainable and technologically advanced transportation options, is forcing manufacturers to rethink their production strategies. In this new landscape, the ultimate goal is to establish a one-piece flow in production—a manufacturing process where each unit moves through the production line without interruptions or backtracking. Achieving this level of efficiency and precision at every stage of production is critical, not just to meet consumer expectations, but also to set new benchmarks in a rapidly evolving industry.
The Evolution of Manufacturing Processes in the EV Era
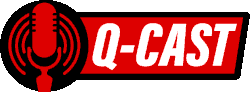
How Digital Twins Can Improve Testing on Electric Vehicles
By replacing the initial tests with digital twin simulations, results can be obtained quickly, and at a much lower cost. Tom Oetjens of Dimensional Control Systems describes the advantages of simulated testing with digital twin.
Listen to more Quality podcasts.
Traditional automotive manufacturing processes, developed and refined over decades, are now being challenged by the unique demands of EV production. Unlike internal combustion engine vehicles, EVs rely on complex battery systems, electric powertrains, and sophisticated software that must work seamlessly together. This complexity requires a level of precision in design and manufacturing that goes beyond traditional methods.
One of the key drivers of this evolution is the adoption of digital twin technology in dimensional engineering. Digital twins are highly sophisticated simulations that create virtual replicas of a product’s design and manufacturing processes. These virtual models integrate real-world data from previous products that utilized similar methods, enabling manufacturers to optimize their operations by predicting potential issues before they occur. By combining real-world data with advanced simulations, digital twins provide an increasingly accurate representation of actual products and processes, making them an invaluable tool for achieving first-time quality in EV manufacturing.
The Role of Digital Twins in EV Manufacturing
The significance of digital twins has become even more apparent with the rise of EV startups. These companies are often in a race to market, eager to showcase advancements in battery technology, powertrains, and innovative interactive features. However, the accelerated development timelines common in the EV sector can lead to the neglect of critical aspects, such as designing a vehicle that can consistently support these innovations. The costs associated with reworking tools, parts, and processes to correct these oversights can be exorbitant, and for some startups, these mistakes have proven disastrous.
By utilizing digital twins, manufacturers can simulate every aspect of the design and manufacturing process, identifying potential issues before they arise. This proactive approach not only reduces the risk of costly errors but also shortens the development cycle, enabling companies to bring their products to market more quickly and with greater confidence in their quality.
The AIAG Advanced Product Quality Planning (APQP) Process
The AIAG Advanced Product Quality Planning (APQP) process provides a structured framework for new product development, with specific steps and critical deliverables designed to ensure that quality is built into every aspect of the product from the outset. The APQP process outlines several essential steps for new product development, each with critical deliverables, including:
- A Well-Defined Assembly Process: This involves creating detailed plans for how each component of the vehicle will be assembled, ensuring that the process is efficient and repeatable.
- A Comprehensive Control Plan: A control plan outlines the monitoring and control methods that will be used during production to ensure that the product meets all quality requirements.
- A Robust Design Failure Modes and Effects Analysis (DFMEA): DFMEA is a systematic approach to identifying and addressing potential failure modes in the design of a product, helping to prevent issues before they occur.
- Tolerance Studies that Support Geometric Dimensioning and Tolerancing (GD&T): GD&T is a system for defining and communicating engineering tolerances, and it plays a critical role in ensuring that parts fit together correctly and function as intended.
By adhering to the APQP process and incorporating digital twins for a two-way data exchange, dimensional engineers can gain deeper insights by studying issues from multiple perspectives. This holistic approach to product development and manufacturing leads to greater potential for improving both products and processes, ultimately enhancing the overall quality of the final product.
Challenges Faced by EV Startups
While the APQP process and digital twin technology offer significant advantages, many of today’s EV startups face challenges in fully integrating these tools into their operations. One of the most common mistakes is a focus on GD&T at the expense of a more comprehensive dimensional engineering process. While GD&T is an important aspect of ensuring that parts fit together correctly, it is only one part of a much larger picture.
Dimensional engineering involves the coordination of all aspects of a product’s design and manufacturing, from the initial concept through to final production. This includes not only the application of GD&T but also the alignment of all components and systems to ensure that the vehicle functions as intended. Unfortunately, this level of detail is often overlooked by EV startups, leading to delays in the launch of production (SOP) dates and other issues that can significantly impact their ability to compete in the market.
The Importance of Datum Coordination
One area where many EV startups fall short is in the coordination of datums within the dimensional engineering process. Datums are the reference points used in GD&T to ensure that all parts are aligned correctly. Without proper datum coordination, even the most well-designed components can fail to fit together as intended, leading to issues with the final product.
While GD&T is a powerful tool for ensuring that individual parts are manufactured to the correct specifications, it cannot address the complexities of assembling those parts into a complete vehicle. This is where dimensional engineering comes into play. By fully integrating the APQP process and utilizing digital twin technology, manufacturers can ensure that all aspects of the vehicle’s design and manufacturing are aligned, leading to a final product that meets all quality and performance requirements.
The Path Forward for EV Manufacturers
As the automotive industry continues to evolve, the importance of achieving first-time quality in EV manufacturing cannot be overstated. The increasing delays in SOP launch dates among EV startups underscore a troubling lack of attention to detail. However, by fully integrating a comprehensive dimensional engineering process, leveraging the APQP framework, and utilizing digital twin technology, manufacturers can overcome these challenges and excel in an increasingly competitive market.
The transition to electric vehicles represents a significant shift in the automotive industry, one that requires new approaches to design, manufacturing, and quality control. By embracing the tools and processes that have proven effective in other industries, such as digital twins and the APQP process, EV manufacturers can set new standards for quality and efficiency, ensuring that their products not only meet but exceed consumer expectations.
In conclusion, the future of automotive manufacturing lies in the ability to achieve first-time quality through the integration of advanced technologies and processes. As EVs continue to reshape the market, manufacturers must adapt to this new reality by refining their processes, adopting new tools like digital twins, and fully embracing the principles of dimensional engineering. By doing so, they will not only meet the demands of today’s consumers but also pave the way for the next generation of automotive innovation.
Looking for a reprint of this article?
From high-res PDFs to custom plaques, order your copy today!