Quality 101
Understanding the Fundamentals of a Manufacturing ERP System
The common purpose of all ERP systems is to enable operational excellence, profitability and growth.

Quality management system (QMS) functionality within a manufacturing ERP system enables repeatable quality programs by building inspection procedures into the day-to-day operation of the business. Source: DELMIAWorks
The full scope of a manufacturing enterprise resource planning (ERP) system goes beyond the basic roles of accounting, purchasing and inventory control that most people think of. It impacts everyone in the business, from the chief executive to the team on the shipping dock, and today it serves a more important role than ever.
In 2024, the produce-at-all-costs mandate of the pandemic era has given way to a market where production capacity is greater than demand, and attention to detail is paramount. Meanwhile, labor and skills remain in short supply, prices have escalated. By necessity, manufacturers now need to focus on operational efficiency to maintain and grow their profitability. This, in turn, has put a premium on the business automation and detailed data-driven planning enabled by modern manufacturing ERP software.
Overview of Manufacturing ERP Functionality
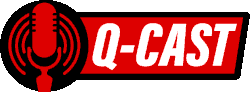
How to Improve Quality with Software
Stephen Bieszczat, chief marketing officer of DELMIAWorks, has seen both good and bad practices on his manufacturing tours. Here he explains software's role in manufacturing trends, how quality professionals can best use software to improve manufacturing processes, and how to tackle your to-do list.
Listen to more Quality podcasts.
At its very core, ERP is the automation of business operations through the collection, organization and processing of data into actionable plans and information. However, manufacturing ERP systems are unique in the areas of resource planning, supply chain management, manufacturing execution and quality control because they provide the features and controls necessary to manage and automate operations that convert raw materials into finished goods. An ERP system built for either a distribution or service business will not support the needs of a manufacturing operation.
To create the backbone of a comprehensive solution for managing their core functions, manufacturers should incorporate the following eight feature sets into their manufacturing ERP implementations.
Finance and accounting are the most fundamental aspects of ERP systems. Profit and loss, cash flow, budgeting, the general ledger, accounts payable, and accounts receivable are all managed by the ERP system’s financial features.
Customer relationship management (CRM) keeps track of customers, prospects, marketing efforts, sales orders and sales history.
Human capital management (HCM) captures and organizes the employee information necessary for payroll, performance management, and training.
Material requirements planning (MRP) and supply chain management (SCM) modules are where the production planning, procurement and inventory control functions reside.
The manufacturing execution system (MES) found on the shop floor is responsible for monitoring production rates and processes.
Quality management software (QMS) provides the system of procedures, records and controls necessary to ensure quality and traceability.
The warehouse management system (WMS) oversees both the flow of raw material into the warehouse and the flow of finished goods out to customers.
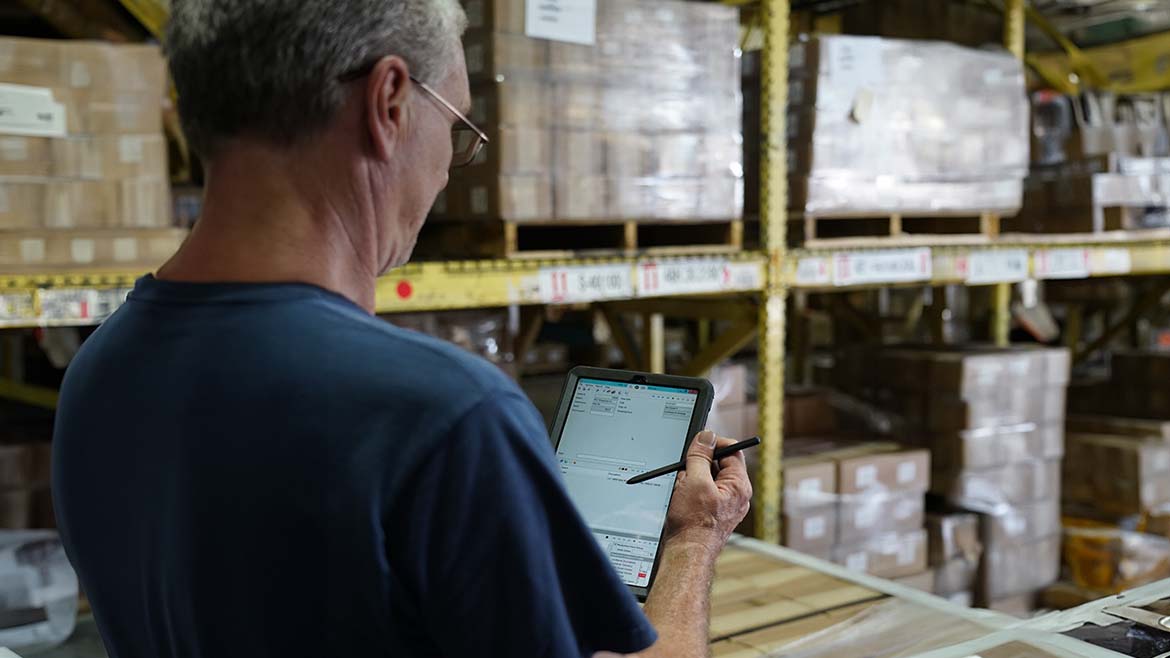
Extracting Value from a Manufacturing ERP System
The common purpose of all ERP systems is to enable operational excellence, profitability and growth. The following five examples illustrate how ERP software drives best practices and efficiency within a manufacturing operation.
Improved Inventory Control
Inventory drives a constantly flowing movement of money: money out for purchasing, money tied up in inventory on hand, and money freed up as finished goods are shipped to the customer. Manually controlling inventory can overwhelm even a well-designed process, which is why automated inventory control is considered one the key benefits of an ERP system. In particular, inventory control is immensely improved by end-to-end automation that is aware of in-flow, conversion, consumption, waste, and shipment in real time.
The ability of manufacturing ERP software to control inventory costs is derived from tangible capabilities that automate and proceduralize purchasing and inventory practices. Some key purchasing and inventory capabilities include the ability to forecast raw material needs based upon bills of materials (BOMs) and sales orders, refill and re-order raw materials automatically as they are consumed, forecast finished goods demand based upon on historical demand and sales orders, account for finished goods as soon as they are produced, relieve finished goods as soon as they are shipped, and identify slow-moving and excess inventory items before they become financial liabilities.
Accurate Standard Costs
Most manufacturers operate their businesses on a standard cost model that is used to price their products and plan their profitability. This makes accurate standard costs a core requirement for manufacturing profitability. The challenge is that standard costs are based on a range of inputs, from materials to production rates to labor consumption. Moreover, these factors change over time.
Therefore, knowing actual production costs and how they compare to standard costs is essential to managing profitability. MES software can be used to measure production costs in real time by capturing data from sensors and smart machines about production rates, scrap rates, material, machine and labor resource consumption, and other factors. These actual costs are documented job by job and then can be compared to standard costs. This allows for adjustments to be made based upon actual events, such as updating standard cost for actual profit margins and/or revealing issues that have crept into the production process and need to be corrected.
Optimized Scheduling
The availability and capacity of machines and labor ultimately determine a plant’s capacity to produce revenue. Underutilized machine capacity due to scheduling inefficiencies and unplanned downtime reduces a plant’s effective capacity and ability to produce profitability.
However, scheduling is a complex, constraint-based exercise based on multiple factors—including demand, availability of raw materials, availability of tools and equipment, required delivery time, production rates—that all become part of a complex calculation. Often even best-case manual scheduling is beyond the capabilities of the production management team, and companies have to settle for just good enough scheduling based on a rough estimate of optimized production.
By contrast, automated scheduling supported by real-time production monitoring allows the ERP system to consider all constraints, at all times and quickly optimize schedules by taking fully into account factors. In this automated environment, schedules can be developed or updated in minutes based on accurate, up-to-the-moment insights on when machines, raw material and labor are available.
Enhanced Quality Control
Creating a defective part and then producing a new part to replace it effectively doubles production costs. For a typical $20 million producer with a 2% defect rate, this can amount to $600,000 per year in the cost of poor quality. Using automation to catch defects early in the process not only improves profitability; it also reduces product liability issues while ensuring downstream customer satisfaction.
Quality management—supported by material reviews, process monitoring, and inspections—is the institutionalization of inspections and the documentation of measurements and results. Like all essential disciplines of the manufacturing operation, it requires broad access to information and a holistic view of the business to be comprehensive and preventative. For instance: Are the raw materials in compliance? Is the tooling and equipment in tolerance? Is the rate of production slow or fast? Did in-line inspections take place as required? Did a properly trained operator conduct the inspection? These are just a few examples from a very long list.
QMS functionality within the ERP system enables repeatable quality programs by building inspection procedures into the day-to-day operation of the business. With a QMS module in place, workflows ensure inspection takes place before downstream process steps occur. Process trends are monitored, and alerts are triggered before they become issues. Inspection results are recorded for root cause analysis and customer documentation, and corrective action programs are documented and enforced. Additionally, statistical process control (SPC) analysis enables manufacturers to increase production rates without introducing quality issues.
Superior Customer Service
The ability to provide outstanding customer service is an often-overlooked benefit of ERP systems. Timely and accurate customer service drives the ability to charge full price and win repeat business. Being able to quote accurate delivery times, update customers on work in progress, meet delivery dates, and deliver quality products ensures repeat business. And available information, scheduling flexibility, accurate labeling, and quality packaging all contributes to delivering top-grade customer service and making a manufacturer easy to do business with.
CRM is a core module here, since it provides a 360-degree view of the customer: what they purchased in the past, what they have on order, future orders, payment history, and financial terms. This functionality complements the advantages of ERP manufacturing software for inventory control, costing and scheduling to enable the last mile of customer service. For example, real-time production data allows service agents to provide on-demand answers to questions about lead times, work in progress, and delivery dates. Similarly, the financial system gives agents information they need to immediately respond to inquiries about accounts payable, accounts receivable, and invoices.
At the same time, electronic data interchange (EDI) brings convenience by enabling manufacturers to conduct business digitally, especially with larger, more sophisticated customers.
Conclusion
These are just five examples of how an ERP system helps manufacturers manage profitability and growth. There are many more, such as quoting and estimating, warehouse management, and logistics.
By implementing an ERP system designed for the specific requirements of manufacturers, companies gain both the tools necessary to run full throttle in boom times and the visibility and control required to operate with precision during periods that demand it.
Looking for a reprint of this article?
From high-res PDFs to custom plaques, order your copy today!