Management | Value of Quality 2-part Series
The Price of Excellence: Understanding the Value of Quality, Part 1
When a company makes quality a primary goal the benefits outweigh the risks.

Image source: Milos Dimic / E+ / Google Images
Quality consistently ranks among organizations’ foremost competitive priorities and is a prerequisite for success in the global marketplace. Firms that want a competitive edge do it by delivering products that meet customer needs and function as intended. Despite the long-standing emphasis on the importance of quality in business, its actual contribution to business performance has been relatively unrealized. Quality is often the first department that gets de-prioritized in the midst of company financial stress. Oftentimes, it is viewed as an overhead expense that can be decentralized into other departments as an attempt to save money. Poor short-term decisions around quality lead to big financial, customer relationship, and work force morale issues down the road, leaving companies in a state of risk that infuses throughout the company and into the customer base. In fact, quality is the foundation for a competitive advantage, even when a firm’s immediate focus may shift towards concerns like speed-to-market, cost reduction, and other operational considerations.
To achieve high growth rates and customer satisfaction, organizations need to proactively anticipate and tackle emerging challenges in the quality of their products or services. This entails adopting a holistic perspective on the interplay between cost, quality, and outcomes. Rather than considering these factors in isolation as most companies do, organizations should recognize the interconnected nature of cost (encompassing all expenses related to product delivery), quality (striving for optimal results), and outcomes (financial reimbursement influenced by exceptional quality at reasonable costs). This perspective versus the traditional cost-centric approach is a more comprehensive framework that incorporates both quality and outcomes, allowing organizations to position themselves strategically in the business landscape and drives cost management, product quality, and overall business success.(1)
Harmonizing Quality Goals with Business Strategies
Management
Related Article
The mission of the quality function cannot be developed in isolation from the mission of an organization, but instead, must be closely aligned and inseparable from the overarching mission and strategy of the organization. Many organizations develop their quality management system and quality objectives in isolation from their business strategy.
Overall business goals and quality strategy should be on the same roadmap in the organization and closely aligned. The interconnectedness of quality and other business goals is a fundamental concept in quality management and organizational excellence. Quality is an investment that is expected to produce benefits later, not an expense for an organization. Companies that invest and focus on quality will not only recover expenditures but will enjoy great benefits within the organization.
Addressing the need for quality resources within appraisal costs is a strategic move for an organization to take. When a company makes quality a primary goal the benefits outweigh the risks. When quality takes a secondary role within an organization, the company often faces internal and external failures that impact costs. When contemplating quality investments, two key investment expenditures usually emerge, the Cost of Good Quality that is taking a proactive approach and Cost of Poor Quality which is usually a reactive approach.(2)
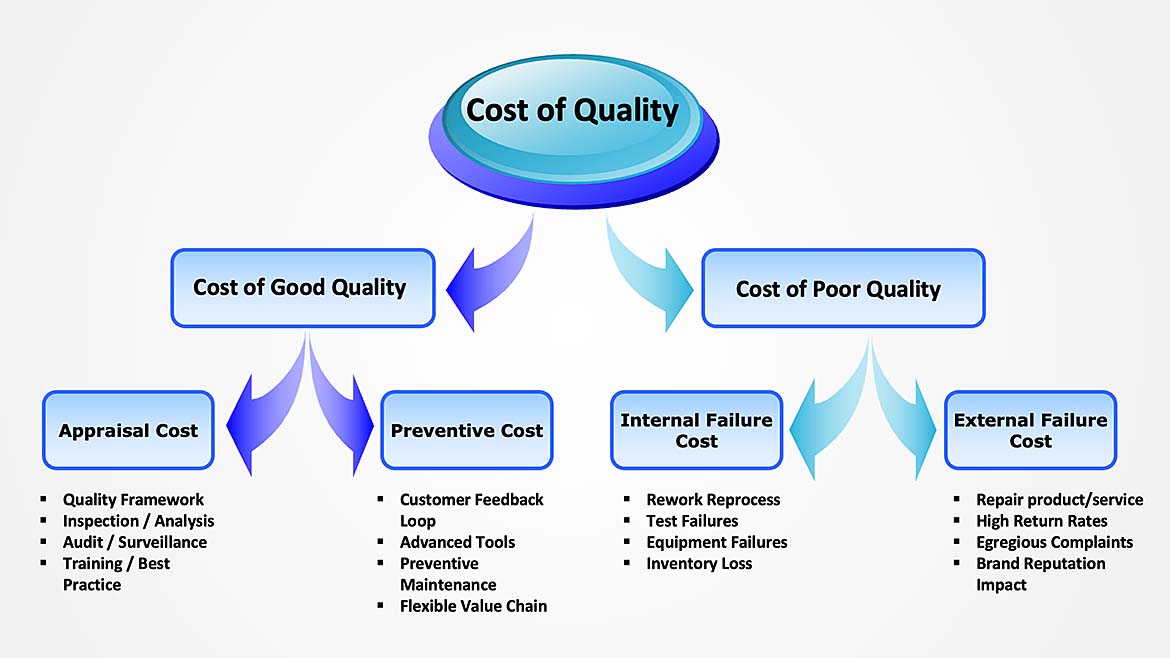
Cost of Good Quality usually leads to understanding role of quality and how it’s a preventive measure in an organization versus a reactive activity. Integrating quality into the appraisal cost of a project is a proactive approach that contributes to project success, cost efficiency, and overall organizational effectiveness it allows quality to be at the forefront of a project versus at the tail end. Investing in quality early in the project life cycle yields substantial benefits in terms of cost savings, customer satisfaction, and long-term success.
Investing in prevention costs is a strategic decision that aligns with the principle of avoiding problems before they occur. While prevention costs involve upfront investments, they result in long-term benefits by reducing overall project costs, improving quality, and increasing the likelihood of project success.(2)
Cost of Poor Quality leads to quality not being invested in or a divestment of resource and time. It’s important to note that reducing investment in the quality department should be approached with caution. Quality is often a critical factor in maintaining customer satisfaction and business success. Always weigh the potential benefits against the risks before making significant changes. However, whether it’s a pause or a just being unaware always consider consulting with quality management professionals or experts who can provide guidance on how to make changes without compromising overall quality. Transparent communication is crucial. Clearly communicate the changes to the quality department and the reasons behind them. Address concerns and ensure that employees understand their roles in maintaining or improving quality.(2)
The cost of poor quality results in internal failure costs due to the need for mitigative and corrective actions within an organization. Assess the potential risks associated with divesting in the quality department. Develop a risk management plan to mitigate any negative consequences. Assess the current state of the quality department. Identify strengths, weaknesses, opportunities, and threats. Understand the impact of potential changes on product/service quality and customer satisfaction. Internal failure costs are expenses incurred to address defects, errors, or quality issues before a product or service is delivered to the customer.(2)
External failure costs are expenses incurred after the product or service has been delivered to the customer, and these costs are associated with addressing issues that occur outside the organization. As a business owner, you are responsible for bearing the costs of product recalls. In the worst-case scenario, you may have to deal with lawsuits. For this reason, companies cannot ignore or overlook the importance of quality management.
The exploration of the Cost of Good Quality and the Cost of Poor Quality underscores the pivotal role that quality plays in organizational success. Embracing quality as an investment to a business enhances project success, efficiency, and overall effectiveness. Investing in prevention costs aligns with the strategic goals of averting issues before they arise, fostering long-term benefits, and increasing the likelihood of project success. A reduction in quality investment raises concerns about potential divestment of resources and time, posing risks to customer satisfaction and business success. It is advisable to approach such decisions cautiously, seeking guidance from quality management professionals and ensuring transparent communication with stakeholders. The evaluation of internal and external failure costs emphasizes the critical importance of maintaining robust quality management practices to avoid corrective actions, mitigate business risks, and uphold customer satisfaction. In this dynamic business landscape, prioritizing quality is not just a cost-saving strategy but a fundamental aspect of sustainable organizational success.
References
- https://www.ahrmm.org/resource-repository-ahrmm/cqo-metrics-100114-1
- The Certified Manger of Quality / Organizational Excellence Handbook, Russell T Westcott, Third Edition, 2005
- (https://www2.deloitte.com/us/en/pages/consulting/articles/quality-engineering-and-testing-trends.html)
- https://www.gbscorporate.com/blog/why-quality-matters-more-than-ever-in-business#:~:text=Higher%20profitability&text=In%20fact%2C%20high%20quality%20produces,defect%20prevention%2C%20profitability%20will%20improve.
- https://www.mckinsey.com/industries/life-sciences/our-insights/making-quality-assurance-smart#/
- https://www.workwithloop.com/blog/roi-and-qa-why-quality-assurance-is-a-good-investment
- https://www2.deloitte.com/us/en/insights/topics/analytics/a-revolution-in-data-driven-quality-improvement.html
Looking for a reprint of this article?
From high-res PDFs to custom plaques, order your copy today!