Measurement
Maximizing Precision: How to Care for and Integrate Your Handheld Gages
Quality control is crucial for meeting high product standards, and handheld gages are key to achieving such precision. But how exactly do these tools ensure accurate measurements?

The I-Wave2 from Marposs is a rechargeable wireless gage designed for dimensional inspection in the workshop environment. Image Source: Marposs
Dave Leboeuf, product manager at Fowler High Precision, emphasizes the importance of strict manufacturing specifications for handheld gages. Each gage is built to very strict specifications to ensure accurate measurements, and higher-end gages are often accompanied by setting masters. These masters help both calibration and the accuracy of measured readings. Regular, thorough inspections and calibration of these gages are needed to maintain their accuracy over time, Leboeuf says.
Keeping Gages In Check
Whether it’s a standard yearly check, an adjustment based on usage, or integrating shift-level practices, calibration schedules should be flexible yet systematic, experts say.
Leboeuf suggests a general rule of thumb for gage calibration. “The rule of thumb is once yearly, but this depends on use. If your gage is being used all day, every day you may wish to have it calibrated more often, [such as] every six months or less.”
Peter Dow, sales and engineering manager at Dow Gage, a division of Sirois Tool, calls for a tailored approach, aligning calibration schedules with specific operational needs and quality assurance protocols. “This should be determined by using the company’s quality program,” he says. “Obviously, the amount of use of the gage on the shop floor should be a factor to determine inspection intervals,” he says.
Michael Jeffers, Marposs product manager, TESTAR Division, offers insight into the calibration practices for Marposs's I-Wave2 probe. While factory-calibrated, Jeffers notes the necessity of regular zeroing at the shift level. While min/max masters are not essential for calibration, they are beneficial in verifying system accuracy. Jeffers points out that this practice can notably reduce the costs associated with frequent calibrations.
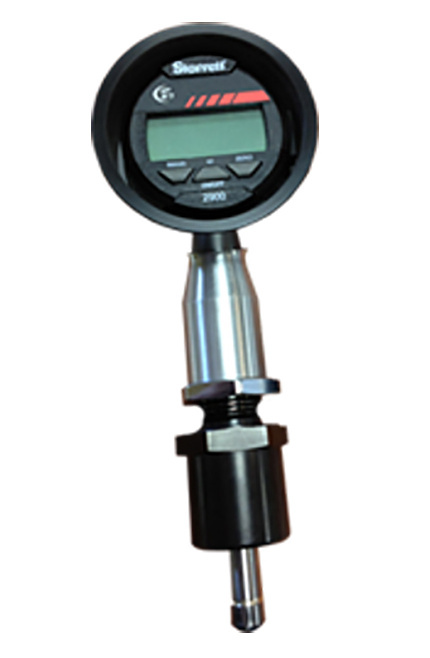
Polished aluminum forging with steel components machined to receive ANSI/AGD Group 2 dial indicators Image Source: Dow Gages
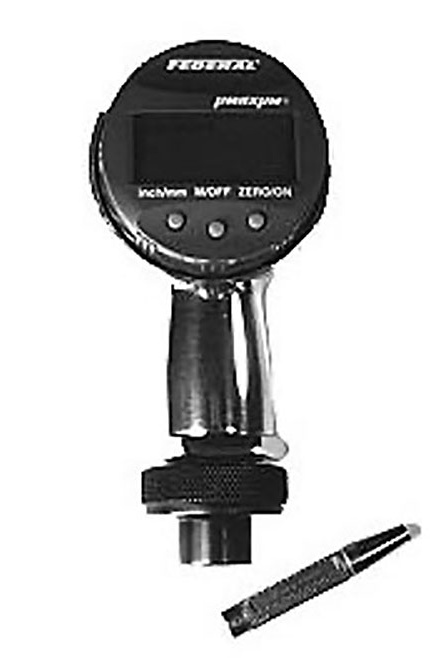
This example features the “hand held” TĀCOMP Stub gage with a Special Stage Set and Setting Master for checking position of taper on a large military projectile. Source: Dow Gages
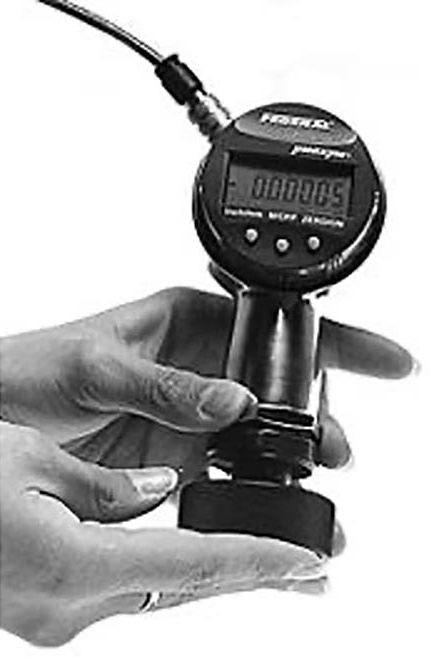
The TĀCOMP Stub shown here is customized to check the angle of taper on a small machine spindle quill shank. The gage is set to “0” with a Taper Plug Set Master which replicates the male taper on the quill shank. Source: Dow Gages
In addition to calibration and inspection, simple practices like regular cleaning, careful handling, and proper storage significantly contribute to the longevity and accuracy of these tools. By adhering to these best practices, manufacturers can maintain the integrity of their quality control measures, ensuring that their products consistently meet the high standards of precision and quality.
“Keep them clean,” Lebouef advises. “Many gages now are water and dust-proof, which allows them to be subject to harsh environments and still work correctly, but they should be kept as clean as possible anyway.”
This practice ensures that even in tough conditions, the gages maintain their accuracy and functionality.
Dow says that, while durable, gages should be protected from environmental damage and wear.
“They should be handled and cared for as any other precision equipment,” he says. “For obvious reasons, all gaging contact surfaces should be wiped or blown clean of chips, etc., before use in the next part to be inspected. When not in use on the factory floor, the gage should be stored in a clean, dry cabinet or drawer.”
Jeffers outlines a simple yet effective maintenance routine. “Simply wiping down gages, eliminating any chip and coolant buildup, and maybe lightly cleaning with denatured alcohol in case of swarf buildup is all you really need,” he states. Jeffers also highlights the importance of proper benchtop space and storage structures to minimize potential damage to the gages.
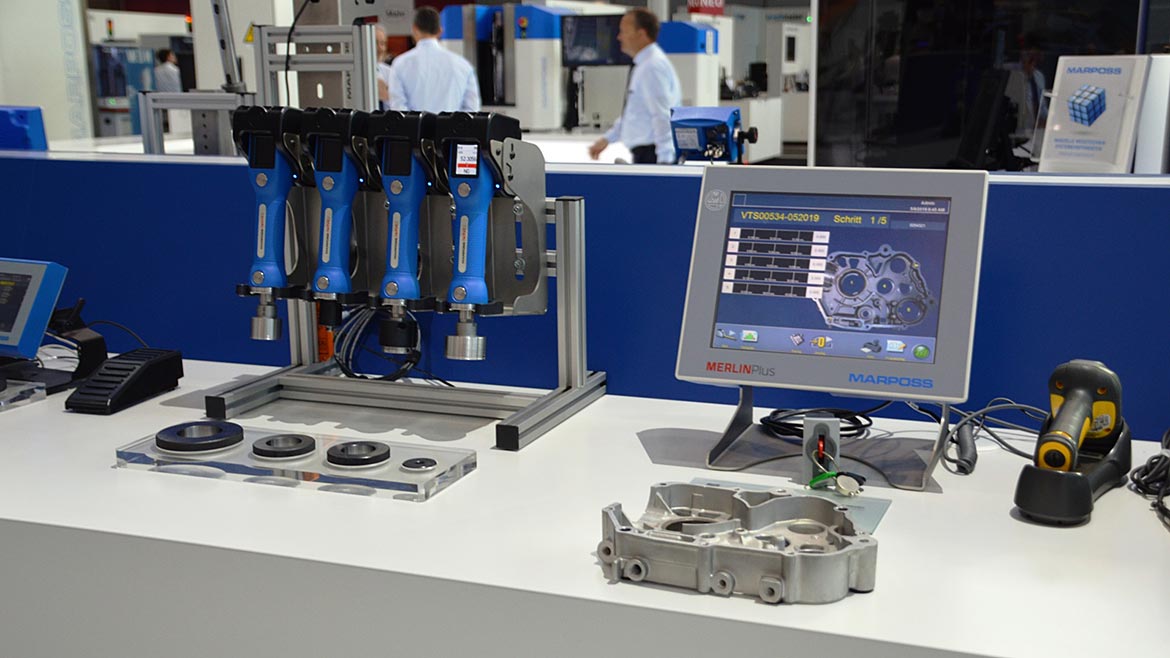
Marposs I-Wave2™ Merlin™ gage computer and guided sequence. ource: Marposs
…And Integrated
Integrating handheld gages with software boosts the accuracy, speed, and efficiency of data collection and analysis, leading to better quality tracking, reduced errors, and more informed decision-making, experts say.
Digital electronic indicators in today’s gages often have the capability to send statistical process control (SPC) data either through wire or wirelessly to data collectors. This data is then analyzed by quality control and metrology staff in the shop, facilitating a more efficient and accurate data analysis process.
Connecting handheld gages to software eliminates recording errors and the need for manual writing, Leboeuf notes.
“No recording errors, no writing,” Leboeuf says. “[You can] enter right into an Excel sheet, connect to a phone or tablet. It’s a big time and error saver, and it’s fast.”
Jeffers highlights the strategic advantages of connecting gages to SPC software. The integration allows for statistical examination of the data, helping to determine necessary adjustments to maintain control over the manufacturing process.
“By connecting gages to SPC software, operators can send inspection data to networks for quality tracking,” he says. “Tool compensation signals can also be sent to the machine (to account for tool wear) and prevent reject parts from being made. Customers can also examine this information statistically and help determine when adjustments are necessary to keep the process under control.”
The integration of wireless data transmission, digital read-outs, and guided inspection processes in handheld gaging tools marks a significant leap in the efficiency of quality checks in manufacturing. They improve the speed and accuracy of measurements and also streamline the entire quality control process.
Leboeuf highlights wireless data transmission as a significant innovation. This feature allows for direct data entry into software like Excel and connectivity with mobile devices, dramatically reducing recording errors and manual transcription. “It’s a big time and error saver,” says Leboeuf. It streamlines the data collection process, making it quicker and more reliable.
Dow discusses the evolution from mechanical to digital electronic indicators. These digital models offer instant read-outs in decimal inch or millimeter and can transmit data for compilation of SPC data, either wired or wirelessly. Dow illustrates the practical application of this technology in controlling machining operations in real-time, enhancing efficiency on the shop floor.
Wireless gaging technology not only accelerates inspection processes but also eliminates operator error in data collection, Jeffers says. It is also flexible, he says, allowing gages to be used in proximity to or even within the machines, thereby reducing interruptions in the manufacturing process. Moreover, Marposs has incorporated “guided sequence” visual aids, ensuring consistent and error-minimized inspection processes.
Looking for a reprint of this article?
From high-res PDFs to custom plaques, order your copy today!