2024 Quality Plant of the Year: 3D Engineering Solutions
March 1, 2024
2024 Quality Plant of the Year: 3D Engineering Solutions
March 1, 2024

If you’re looking for some 3D scanning work, 3D Engineering Solutions may be the answer. And if you’re looking for reverse engineering, quality control, fixture and tool design, ISO 17025 certified inspection services, and 3D digitizing, noncontact laser scanning, the Cincinnati-based company offers that too.
The company has been described as “close to being a prime lab” by an auditor. They cross train engineers on every piece of equipment, and review 5S and continuous improvement strategies weekly. They also offer a good work environment, letting staff know that if something breaks, they will address it without blame. But most importantly, quality guides all of their work.
“It is our core philosophy,” says JR Hassett, vice president of sales. “We don’t let work leave here until it’s correct.”
Article Index
Related Articles
This leads to happy customers—in about 6,000 projects, he recalled perhaps eight upset customers—and repeat customers too. “When it’s done correctly, they come back,” Hassett says. “They trust us.”
For their high standards and dedication to quality, this year Quality would like to honor 3D Engineering Solutions as our 2024 Quality Plant of the Year winner.
Quality and Customer Satisfaction
Sometimes their high-quality work can lead to some bad news for customers.
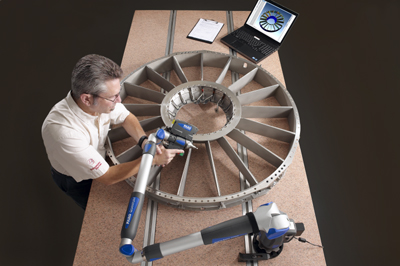
One CT scanning situation showed how 3D Engineering Solutions knew what they were doing. A customer came to them with a job where another company had already done the scanning and measurements, but they needed the work to be ISO 17025 accredited. They redid that job and found all the mistakes the other company had made. Print misinterpretations and slight canning issues lead to totally different results. The customer was happy that these errors were discovered, although not that they had paid for poor work from another company.
Looking for a reprint of this article?
From high-res PDFs to custom plaques, order your copy today!
This level of skill is intentionally developed at 3D Engineering Solutions. They look at someone’s strengths and weaknesses then assign tasks to help the engineers grow. They also do extensive training. A new hire starts with GD&T training their first week and it continues from there.
“Everybody here is trained up to the most proficient level starting from day one,” says Matt Caskey, quality manager.
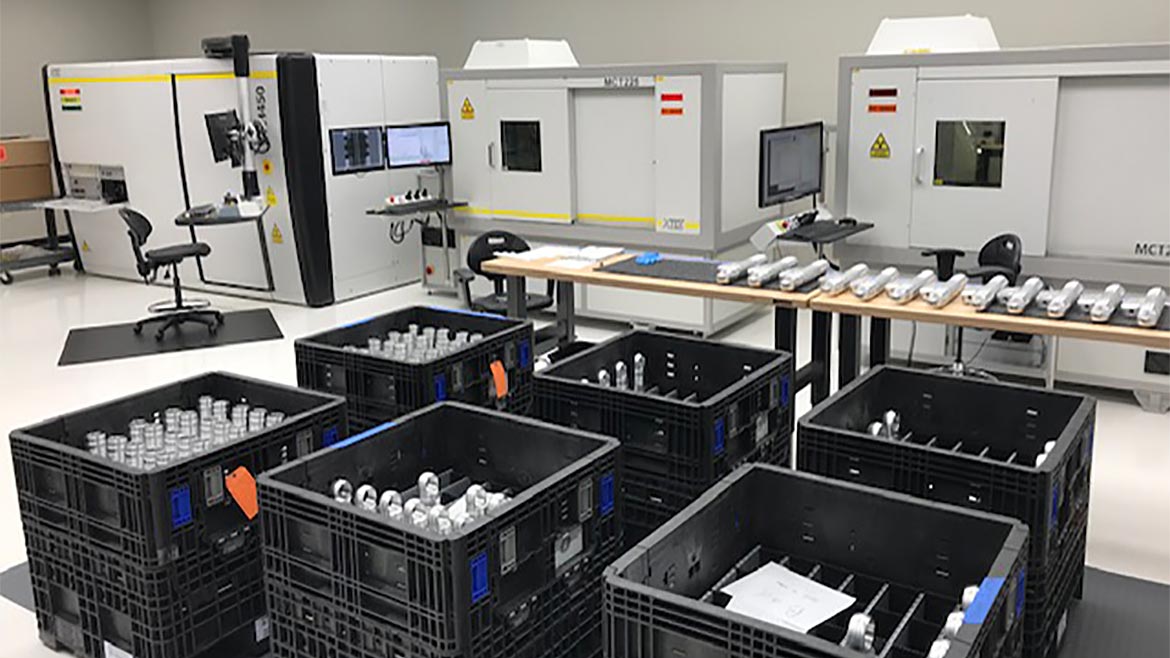
A Culture of Calm
Along with training, the company prides itself on a good work environment, which makes projects easier for both staff and customers.
The company has worked with thousands of customers, in industries ranging from aeronautics to archaeology. Their digital laser scanning services have applications in automotive, motion picture and gaming, tool and die, manufacturing, forensics, medicine, maritime, “anywhere precision digital 3-D modeling is required,” the company says.
Many of these industries require the highest levels of quality, which could lead to high pressure situations. But Rob Glassburn, vice president of operations, says they handle things well despite this. Their internal culture allows more cooperation, less finger pointing.
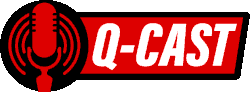
The Secrets to Success from 3D Engineering Solutions
How our 2024 Plant of the Year focuses on customer service, friendly engineers, and a strong work culture to make it the top choice for customers around the globe. Rob Glassburn, VP of operations at 3D Engineering Solutions, explains the company’s environment and goals. To hear more from our Plant of the Year, visit The Quality Show South this May. Rob will be speaking Wednesday, May 1 at 1 p.m. View the agenda here.
Listen to more Quality podcasts.
“We deal with a lot of expensive equipment and a lot of customers as well who are hurried and pressed for time,” Glassburn says. “If something breaks, just let us know.”
It’s not like they haven’t seen it before: “Equipment dropped from two stories high, equipment fell into water, lasers crushed,” Glassburn says. “If you break it, let us know.” This attitude “keeps our guys as less stressed as possible.”
And it also helps minimize customer stress. If their staff can have positive attitudes, it makes customers happier. If the staff felt overworked, this would carry over into customer interactions—and they want good customer-facing engineers.
The service bureau has a small staff, cross trained on every piece of inspection equipment—CMMs, lasers, structure light scanners, industrial CT scanning systems—as well as backup equipment.
Matt Caskey deserves a lot of credit for this environment, says Glassburn. “Matt is able to communicate in a calm manner” rather than shutting down or going off, as some people might. This calm demeanor means that customers are not dealing with additional pressure in meeting deadlines. They try to promote the idea that any issues are not personal, perhaps that person is having a bad day, or even a bad year.
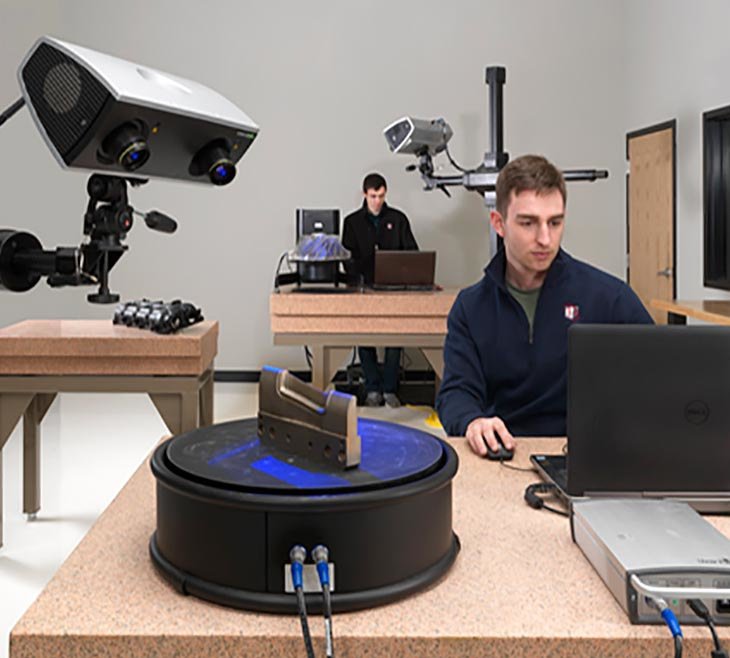
“It’s a people business,” Glassburn says. “It takes experience to get to that level of calm.” People don’t just begin with Matt’s demeanor.
How do they foster this type of environment?
Well, food doesn’t hurt. Since it’s a small organization they offer a family atmosphere. JR Hassett, vice president of sales, makes breakfast for the staff several times per year.
As Glassburn notes, “JR is a great chef. We want people to stay.”
The company also offers a workout room, perhaps another good way to relieve stress.
With their engineering expertise and people skills, staff are able to handle any issues that arise, whether technical or emotional.
“No matter what level you think you are at, in the metrology game, our guys really are experts in their field,” Caskey says. And just as importantly, not everyone can handle things with such grace.
Perhaps you’ve seen this. When questioned, someone might become anxious and withdrawn. Instead, their staff engineers talk things out, relying on “muscle memory” to resolve a situation.
As Caskey says, “Nobody can know everything but we do know what we know. And we validate it year after year with audits.”
The company does yearly ISO 17025 audits to tighten their measurement uncertainty budgets, and their engineers also do proficiency testing on a yearly basis.
This leads them to be competent—but not arrogant—Caskey says.
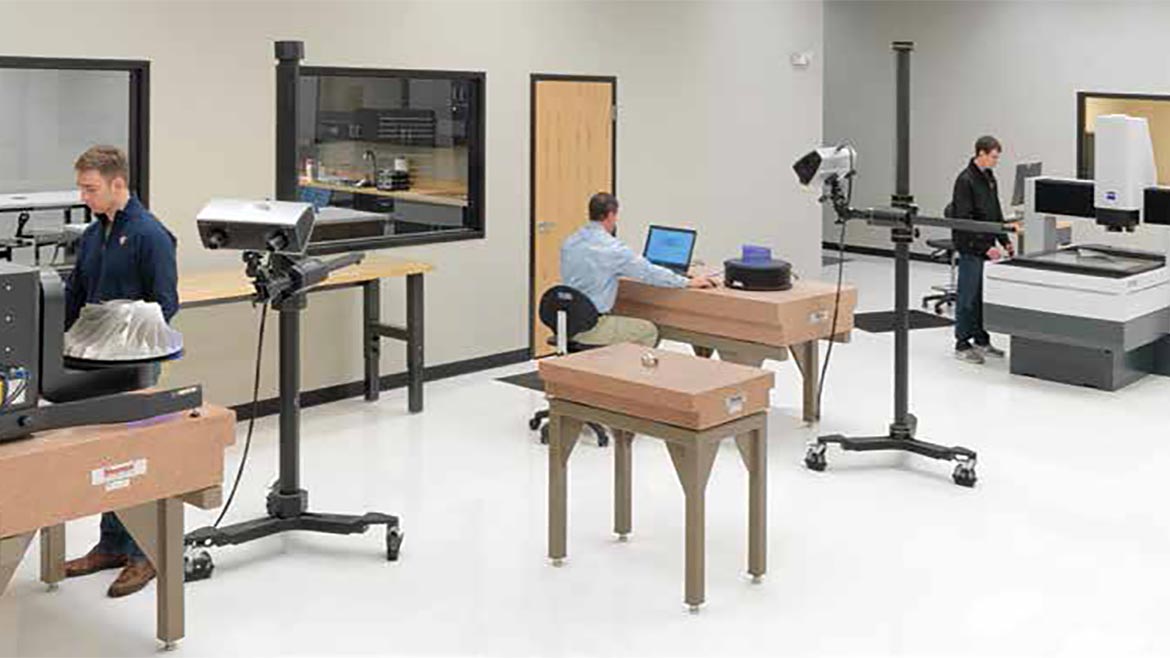
Celebrating
The company knows how to get the job done. They also know the importance of fun.
They know it’s wise to have every area covered in the event someone is out. But they also know that is fun to celebrate birthdays. The day we spoke they had just celebrated a staff birthday with pie and coffee.
The company has appeared on the Quality Leadership ranking in the past, where we noted their excellent work in not missing deadlines even during the pandemic and supply chain disruptions. But their focus on deadlines doesn’t sacrifice quality or even a good atmosphere.
Congratulations to the entire staff and keep up the good work.
Meet Previous Years Winners
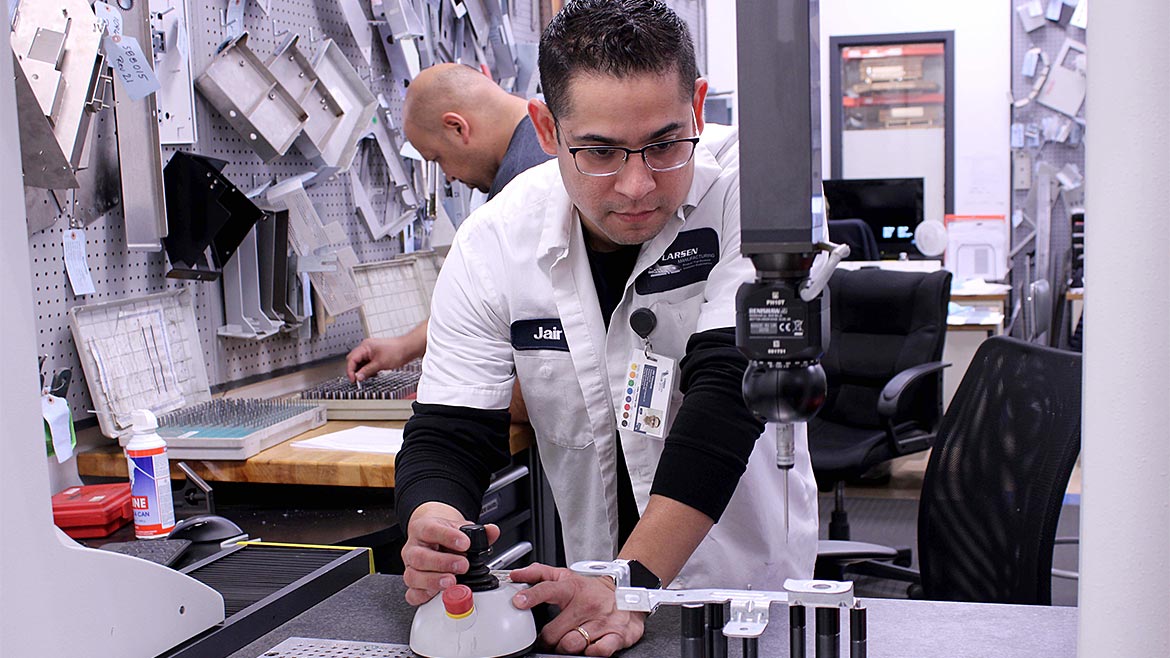
Larsen Manufacturing
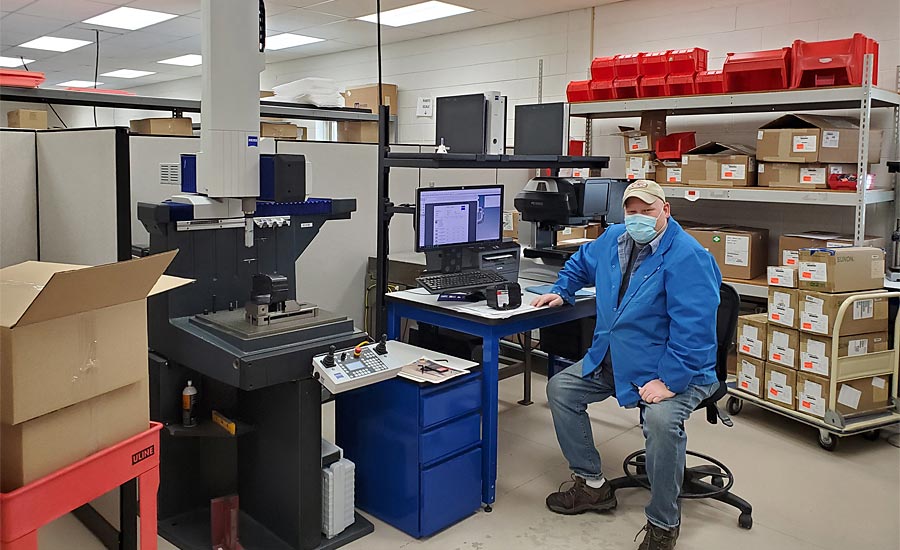
Electromed, Inc.
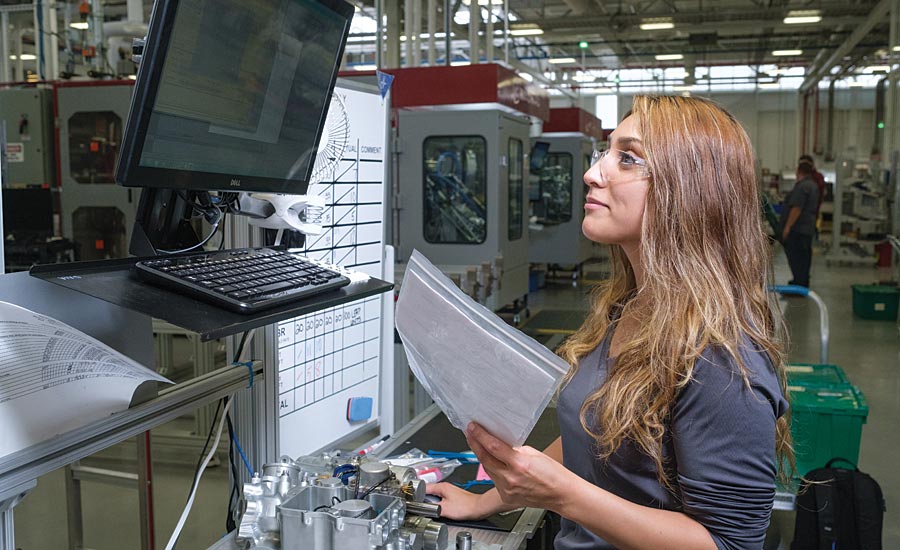
Woodward's Rock Cut