NDT | Leak Testing
Leak Detection’s Crucial Role in Li-ion Traction Battery Production
Manufacturers that routinely challenge their leak tightness testing process will consistently produce products with reliable performance, battery longevity and safety.

All Images Source: INFICON, Getty Images, and Freepik
The future of the automotive industry lies in electric propulsion and many global automakers have chosen lithium-ion batteries to power their vehicles. As new battery plants are commissioned and constructed in the U.S., it’s important for battery manufacturers to incorporate leak testing into their manufacturing operations. Often, the performance challenges, product failures and fires associated with EVs can be traced back to leaks in the lithium-ion EV battery system. These risks can be virtually eliminated with leak detection testing during battery production.
Leak detection is a standard process in the majority of manufacturing operations to ensure products meet high performance and quality standards. For lithium-ion traction batteries, leak detection is imperative for battery performance, longevity and safety, especially the prevention of fires.
There are three main components of EV traction batteries: the individual lithium-ion battery cells, the battery pack, which is constructed of hundreds of battery cells, and the thermal management system, also known as the cooling circuit. During the assembly of lithium-ion battery components, every seam, weld, gasket or joining method presents the opportunity for leakage so small that it escapes observation with the naked eye. Despite their minuscule size, a leak anywhere in the EV battery system can negatively impact the functionality of the entire battery.
EV traction batteries leak tightness test scenarios
During operation, EV traction batteries have cyclic and continuous high charge and discharge rates. These intense and harsh cycles produce constant high levels of stress on the entire lithium-ion battery system, which only strengthens the position for incorporating leak testing in all phases of battery production.
Three failure modes for EV traction batteries can be tied back to very small leaks within the main system components: diminished operating capacity, shortened battery lifespan and fires. Leak tightness testing at the cell and pack level, and for cooling circuits in the battery’s thermal management system, can prevent these all-too-common failures, as well as provide a method to meet rigorous quality standards.
At the battery cell and pack level, it’s critical to perform nondestructive leak detection for electrolyte leakage, as well as liquid water or water vapor ingress in the form of humidity. The concern for water mixing with electrolyte is the creation of hydrofluoric acid, which is inflammable and also attacks the components of the battery to decrease their lifespan.
For the cooling circuit, leak detection is conducted to identify the escape of medium (ethylene-glycol) into the battery pack, where it can short-circuit high-voltage power electronics systems.
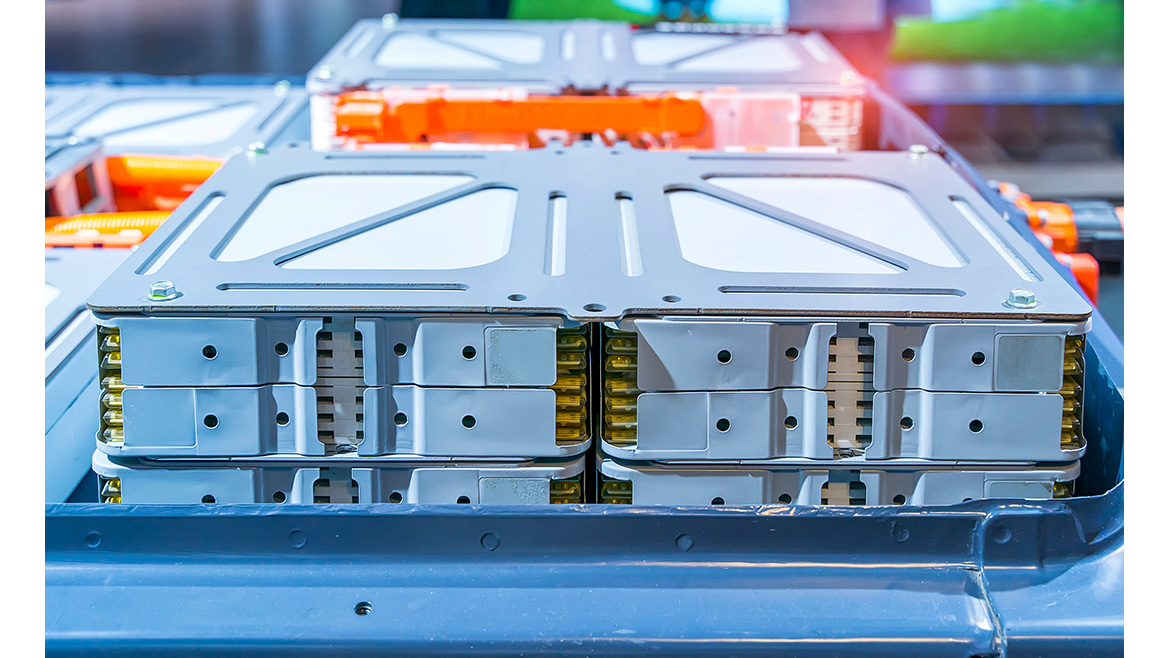
Battery cell leak tightness
In lithium-ion EV battery packs, the battery cells are the repository for the electrolyte. Since the electrolyte is responsible for carrying the ion transmission in the battery, any amount of leaking electrolyte would result in diminished capacity of the cell itself, as well as reduced longevity, and would possibly lead to combustibility, depending on the nature of the leak. These failure modes can be prevented with leak tightness testing during cell manufacturing.
Leak testing during cell production is best carried out in two stages: before the cell is filled with electrolyte to check for any possible leak channels in the cell enclosure, and after the cell is filled with electrolyte to check if the filling port has been sealed properly.
Using a vacuum chamber test, the battery cell housing is placed within the chamber and a tracer gas is used; typically, a helium mixture or a safe blend of hydrogen and nitrogen. During pump-down, or evacuation of the test chamber, any escaping gas can be detected as the test gas migrates into the vacuum chamber. Highly sensitive mass spectrometers are used to capture the measurement information on leak location and size.
Next, when a proven leak-tight cell is filled with electrolyte and sealed, it’s crucial to test the leak tightness with the same vacuum pump system to detect any evaporating electrolyte solvent.
These systems can be incorporated in production lines at end-of-line testing stations with high throughput to detect leaks in a few seconds. When equipped with a multi-chamber design, this leak detection test can be optimized for a batch-testing approach, which generates a high-speed and time-saving in-line testing process.
The system can be used to detect the smallest leaks in lithium-ion battery cells in the region of 0.5 µm to about 5 µm, with the resulting leak rate as low as 5.10-7 mbar·I/s.
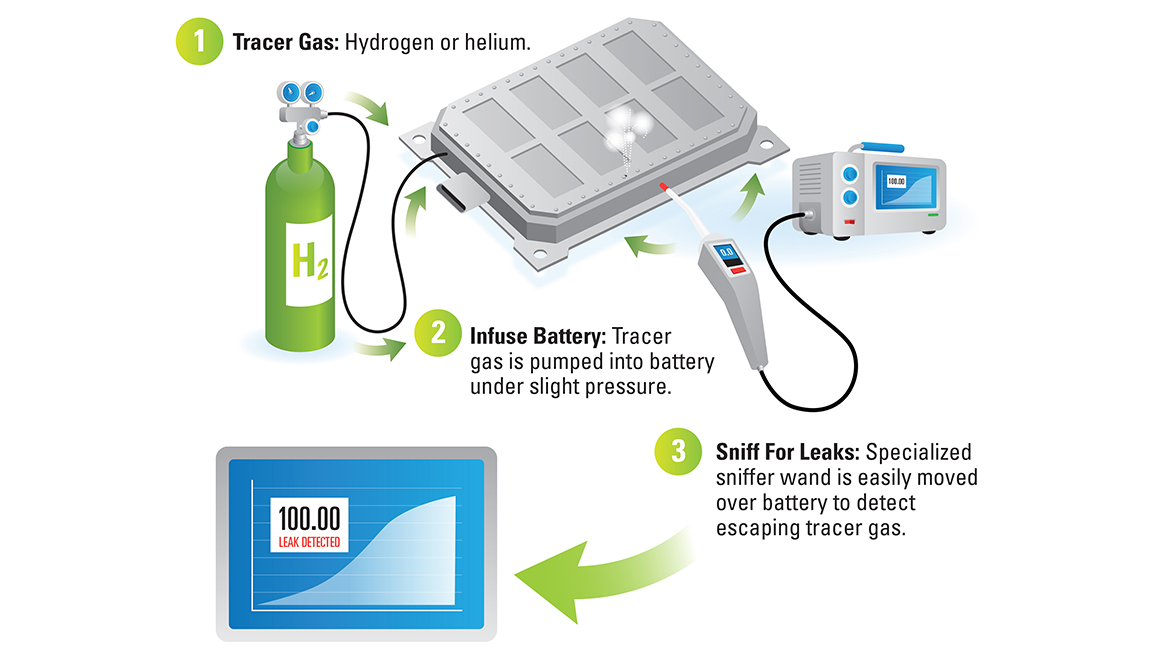
Battery pack leak tightness
In most passenger EVs, including pick-up trucks and SUVs, the battery pack is designed to fit on a platform underneath the passenger cabin in a skateboard design. At the size of a queen-sized mattress, the EV battery pack can leak in approximately 300 places.
Due to its position on the underside of the chassis, EV traction battery packs are susceptible to water ingress with a splash during rain storms, when driving through puddles or when completely submerged in water for about 20 minutes at a boat launch. Therefore, it’s critical for the battery pack to meet a high standard of leak tightness so that, despite any type of exposure to water, the electrical system will be fully functional and not prone to short-circuiting.
Given the large size of the battery pack, leak testing must be conducted with a sniffing tool – manual or robotic – using a tracer gas and a highly sensitive mass spectrometer. To conduct the test, the battery pack housing is filled with the forming gas. As the sniffer tool moves across the battery pack, it will detect a leak outlet channel via the hydrogen phase of the escaping gas. This testing method produces highly accurate, repeatable and reliable measurements, and can detect small leaks, for example, in the 10-4 …10-6 mbar I/s range.
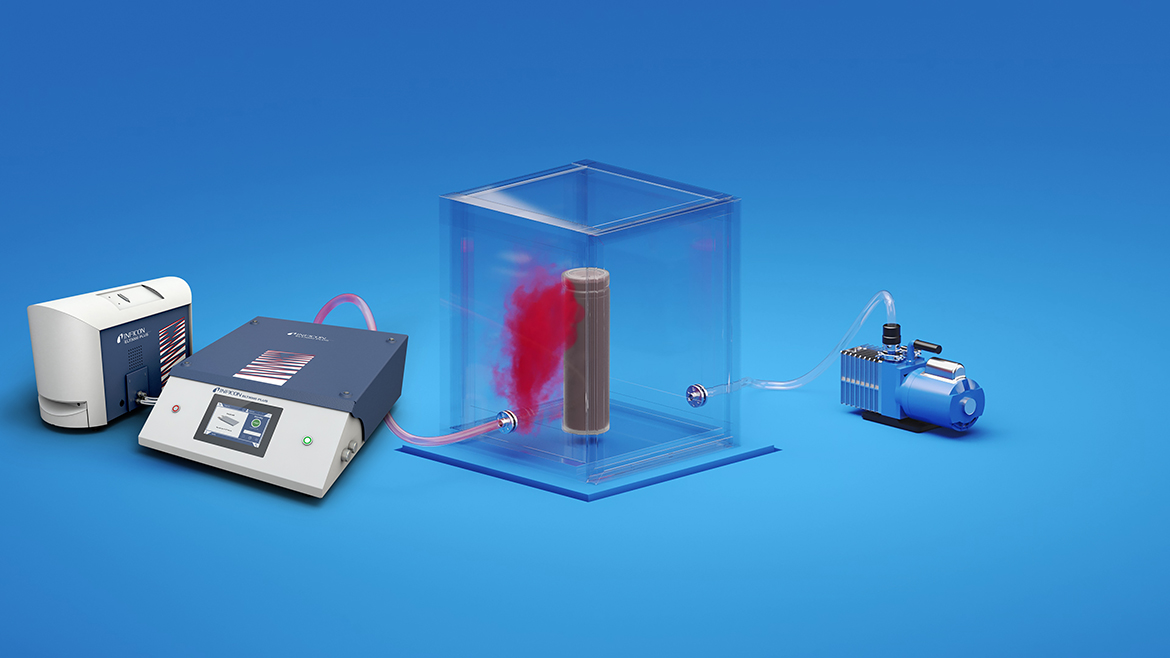
Thermal management system leak tightness
A cooling circuit is an essential component for thermal management in lithium-ion traction battery packs. It regulates the temperature to prevent overheating, which would damage the battery pack and cells, compromising performance and lifecycle, as well as vehicle safety.
Cooling circuits are filled with a mixture of water and ethylene glycol, which possesses the chemical properties to manage the operating temperature. Leak tightness testing is conducted here to prevent loss of medium, in this case, the water-ethylene glycol mixture, which would compromise the function of the cooling circuit and, by extension, the entire battery pack. As previously mentioned, the cooling circuit is surrounded by high-voltage electronics. Any escaping liquid could immediately short-circuit the battery pack, which has the potential to present a multi-layered hazard.
The mechanical properties of the material used to construct the cooling circuit need to be considered when conducting leak testing – steel, copper, aluminum or composite. The material properties of the cooling circuit influence wetting of material with ethylene-glycol mixture and determining when a leak is fully blocked with the cooling liquid. Also, during battery operation, as the temperature of the ethylene-glycol in the cooling circuit significantly increases, its viscosity decreases, which increases the leakage rate. Conversely, when the temperature of the ethylene glycol medium decreases, its viscosity increases, which decreases the leakage rate. The viscosity influences the amount of leakage for open leaks.
Therefore, the fluctuation in viscosity, the influence of the material combinations, as well as the operating pressure and temperature, must be taken into account when setting leak detection parameters.
A best practice for testing leak tightness of a cooling circuit is to start with a rejection limit in the range of 10-3 to 10-4 mbar I/s, with the option to create a usage-specific leak test design. For the cooling circuit, the leak test is best achieved with a sniffer tool using a tracer gas, with the sniffer tool directly connected to a highly sensitive mass spectrometer for reading measurements.
Leak detection: no one-size-fits-all
From the brief description of three leak detection scenarios in lithium-ion traction batteries for EVs, it is readily apparent that there is no one-size-fits-all solution for leak testing. There are many variables for each element discussed: EV battery cells, battery packs and cooling circuits in the EV battery thermal management system. While tests may be similar for each, especially the use of a tracer gas for battery packs and thermal management systems, variables must be accounted for in each test by clearly defining the acceptable diameter of a leak channel, e.g., one that may take three years to produce a droplet that cannot be observed with the naked eye.
For manufacturers to be effective in providing highly efficient lithium-ion traction batteries for EVs, a best practice is to periodically evaluate the quality outcomes of the results of its leak detection test systems to examine whether the actual test results align with the test results they have been presenting to customers. This evaluation is achieved by running a standard “red rabbit” test by putting parts with simulated leaks in their manufacturing process to prove that their systems meet the standards they claim.
For example, by putting a battery pack with a simulated leak in the quality process will reveal the degree to which liquid water ingress is detected at the established measurements. Do the same for battery cells – cylindrical, prismatic, pouch, coin – as well as thermal management cooling circuits to prove their leak testing equipment is performing at optimum levels. If not, go back and evaluate each process to see where adjustments need to be made.
Complacency is the enemy in lithium-ion EV traction battery leak tightness testing. Manufacturers that routinely challenge their leak tightness testing process will consistently produce quality products that meet customer demands for reliable performance, battery longevity and safety.
Looking for a reprint of this article?
From high-res PDFs to custom plaques, order your copy today!