Quality 101
Building Blocks to Improve Organizational Culture
Lay out a road map to achieve organizational excellence and build a culture around it.

Source: Hispanolistic/Vetta via Getty Images
Building and improving a culture of organizational excellence requires a systematic approach. A robust model is required to achieve and sustain its performance goals. Organizations must assess the maturity of their processes and organizational readiness to implement such a methodology before embarking on the journey. An organization should be at least at level 3, Defined Systems Approach, of the Management System Maturity Model to reap the rewards of a culture of excellence.
Introduction To The Capability Maturity Model
Watts Humphrey developed a model of organizational capability some years ago. The model was expanded by Carnegie Mellon into a sophisticated Capability Maturity Model Index. Most organizations are not at the process maturity level to experience the benefit of a systematic culture of excellence. Humphrey’s original Process Maturity Framework and later maturity models focus on transforming the organizational environment in which processes are performed.1 The original CMM was a roadmap of Best Practices in software engineering accompanied by the Best Practices in project and organizational management required to sustain them. Such descriptions provide a sense of how best-in-class processes improve over time. Most of these models, however, give little guidance on the steps required to progress up the maturity levels.
Figure 1 shows the progression of the five maturity levels including the characteristics of each level. This model is a useful tool for organizations to understand their current level of maturity and progression leading to higher levels of business maturity.2 This model defines the levels of organizational system maturity and helps companies evolve an effective culture based on their current level of maturity. Considerations include:
The maturity of the company’s business environment will have an impact on its ability to successfully implement process improvement efforts (either incremental or radical).
Similarly, an effort to improve processes is probably futile if the basic elements that are needed to support effective process management are not in place.
Companies must implement effective quality management and process management systems before any serious improvement initiative is considered.3
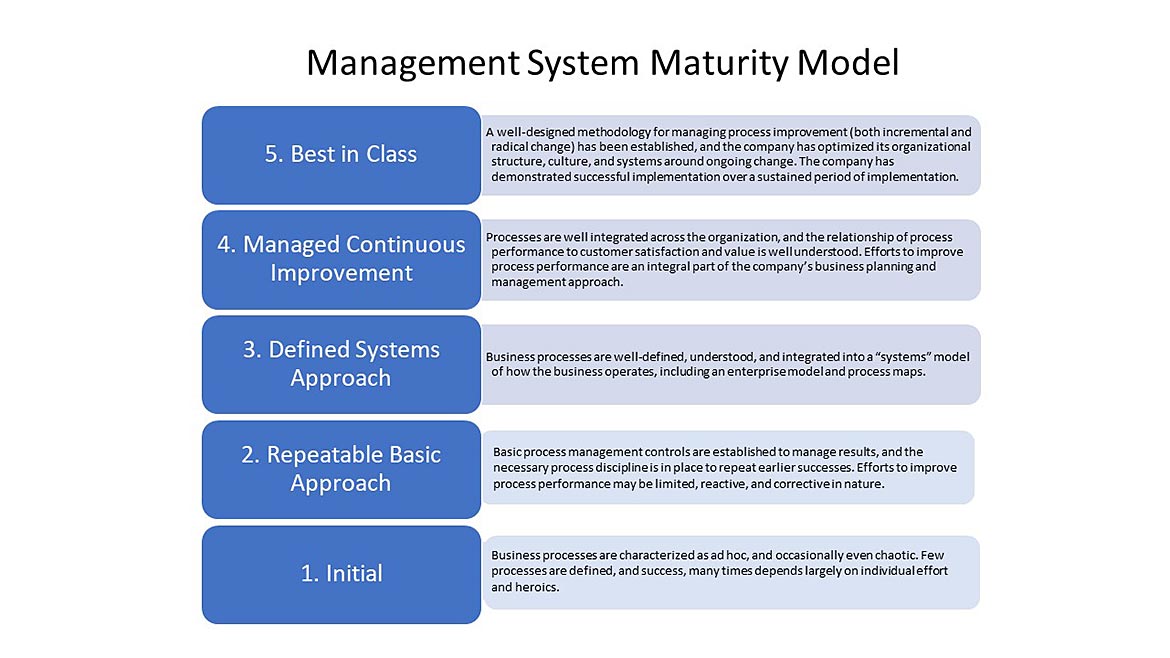
Figure 1: Management System Maturity Model4 (Click on image to enlarge.) | Source: Grace L. Duffy
Begin By Aligning The Organization And The Culture To Meet Strategic Goals
When processes and people are not aligned with the strategic direction of the organization, a culture of excellence cannot be sustained. When there are misalignments within an organization, its processes must be better defined, along with the data used to determine the state of those processes. Figure 2 shows the steps or building blocks required to create and sustain a culture of excellence. Without a strong foundation of alignment to long-term goals, people soon revert to how they did things in the past. Alignment is like a team of people rowing in the same direction. You can have the best boat design, the best paddles, the best rowing techniques, and even the best athletes. When they do not row together in the same direction, these other factors will not matter.
Alignment goes hand in hand with having the right people on the team. As discussed in Jim Collins’s book “From Good to Great,” it is essential to have disciplined people with disciplined thoughts who can carry out disciplined actions. More than good processes are necessary. Start with the “Who” and then progress to the “What.” Without having the right people, many processes that are considered best practices may not benefit the organization. Therefore, it is important to have the right people with goals established and communicated so that there is alignment from the top down throughout the organization. These first two steps in figure 2, Align and First Who, then What, are necessary for improving the organization’s performance.
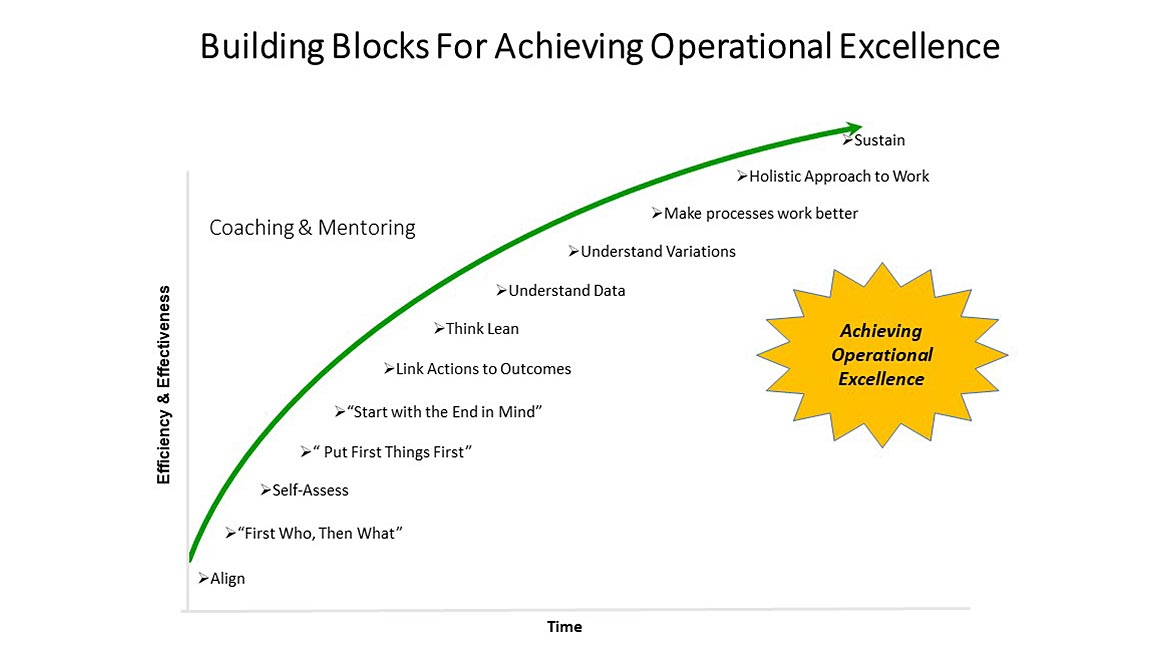
Figure 2: The Building Blocks of an Organizational Culture of Excellence5 | Source: Grace L. Duffy
You cannot improve an unstable system. The first task if you have an unstable system is to stabilize, which is done by aligning teams within an organization. Aligning teams with the core processes they perform drives a stable working system. Then the third step is to continually assess yourself against a set of goals and expectations and see how well you are doing. Adjust as necessary. Participation is a crucial step where everyone in the organization considers how well they are aligned with the mission. The next few steps are about getting a more detailed look at where one can improve by linking actions to outcomes. And then introduce how processes can be enhanced with a more in-depth understanding of data and variations. Improve operations and sustain them over time. The last step is critical. Given the amount of effort spent to establish organizational excellence, you must ensure it is sustained. Mindful leadership, which is part of a culture of excellence, is crucial to ensure that everything works together and that you have an optimal system.
Lay out a road map to achieve organizational excellence and build a culture around it. The Building Blocks of Organizational Culture are a combination of process and people. We have tested this approach in a large Northern Virginia hospital system by starting in a small department. The model was then successfully used to create a culture of excellence across a large corporate defense contractor.
References:
- BPM and Organizational Maturity, Curtis, Bill and Alden, John, BPTrends Column, October 2007
- Van Nuland, Yves, and Duffy, Grace L, Validating a Best Practice: A Tool for Improvement and Benchmarking, Routledge Productivity Press, New York, New York, 2021 pgs 23 – 25.
- Ibid.
- From Quality to Business Excellence: A Systems Approach to Management, Charles G. Cobb, Quality Press, 2003. p. 184
- Le, Hung, and Duffy, Grace L., Human-Centered Lean Six Sigma: Creating a Culture of Integrated Operational Excellence, Routledge Productivity Press, New York, New York, 2023, in final draft 2/14/2023 Chapter 4
Looking for a reprint of this article?
From high-res PDFs to custom plaques, order your copy today!