Management
2022 Quality Plant of the Year: Larsen Manufacturing
Larsen Manufacturing is an industry leader in quality systems and quality assurance.

All Images Source: Larsen Manufacturing




Larsen Manufacturing is a quality powerhouse, with quality metrics to be proud of, surpassed revenue goals, and customer awards—and the entire team has worked hard to get where they are today.
The company began a concentrated improvement journey more than seven years ago after one of their largest customers said all orders would be on hold until quality issues were resolved.
Article Index:
The newly hired quality director and top management evaluated how to improve customer relationships. They came up with a plan to address issues facing this customer and oth-ers. In addition, the entire organization realized that quality is everyone’s responsibility. Thus, more detailed audits, team building projects, and participation from production, engi-neering, and the tool room were added for support.
With a renewed focus on quality, the business began to perform at the highest levels—so much so that this past October the same customer awarded Larsen their Small Business Award.
For their dedication to quality, Larsen Manufacturing (Mundelein, IL) has earned our 2022 Quality Plant of the Year award.
Meeting And Exceeding Quality Goals
Larsen is IATF 16949:2016/ISO 9001:2015 certified. The company serves a diverse range of markets, including medical, industrial, automotive, energy, electronics and consumer products. The company offers precision sheet metal fabrication, metal stamping, powder coating and assembly services. They are able to provide turn-key metal manufacturing from design, through prototype, part production and assembly.
As with many manufacturers, the last two years have been problematic. And in 2022 these problems continue for a variety of reasons. Although Larsen has experienced supply chain issues, they are doing their best to secure materials and manage customer demands. In addition, keeping staff healthy during the pandemic has been a high priority. Despite these hurdles, there has been positive change during these times. “The growth the past couple of years for Larsen has been exponential. It’s a good challenge, but a challenge nonetheless,” says Sheri Dorman, stamping quality manager.
While headquarters are outside Chicago, Larsen Manufacturing also has a sister facility in El Paso, Texas. The two sites work closely to share ideas, implement audit strategies and correlate measurement methods. When El Paso develops new quality initiatives, the Mundelein team adopts them as well.
Quality metrics remain strong at each location. The company tracks cost of poor quality (COPQ) and continues to exceed their goals. The threshold was set at 0.4% of sales. The current corporate COPQ is 0.30%. It was 0.35% in 2020 and 0.48% in 2019.
Both Sheri Dorman, stamping quality manager at Mundelein, IL, and Alena Kraskovska, corporate quality assurance director, say making a quality part the first time makes things easier for everyone, including the production team, the quality staff, and the customers. They also emphasize that all team members are key to good quality.
“We try to empower employees,” Kraskovska says, “not to just press a button and run a machine.” If the production team sees an issue and wonders if something is wrong, they are encouraged to ask about it and bring their concerns to the leads, supervisors, and quality. They cultivate an atmosphere of openness with team members.
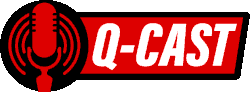
2022 Plant of the Year: Larsen Manufacturing
The team at Larsen Manufacturing appreciates the importance of continuous improvement. Alena Kraskovska and Sheri Dorman discuss challenges at the company, working with ASQ, and their quality philosophy.
In addition, continuous improvement projects are one of the methods of achieving high quality. Dorman notes that the stamping division in Mundelein has had at least one continuous improvement project per quarter for the past two years. This pace was only possible once they stopped having to react to problems. It allowed them to prevent problems before they cropped up.
“We’re constantly looking into areas to improve,” says Kraskovska. “Some projects take five or six months to complete, some are easy and simple. Now, instead of constantly firefighting, we have time to think about improvements and plan.”
While quality metrics continue to trend in the right direction, the employee attitude towards improvement is also on the rise. Since the improvements were implemented, the culture of the company has also changed. In the past, the team might have said, “We’ve always done things this way,” Kraskovska says, but this mentality has changed. “I haven’t heard that as much,” she notes. Instead, people are excited to share ideas and participate in solving problems.
Quality is contagious when changes are made, and the improvements are seen. As Dorman says, “People get excited about projects which in turn has created good morale and a desire to help. This has made for a better work environment and happier customers.”
The team knows that quality is a practice, not something to cross off the list. Along that note, Dorman’s email signature quotes Aristotle: “Quality is not an Act, it is a Habit.”
“Quality isn’t just the quality department,” says Dorman. “Quality involves everybody. That’s what we teach and how we mentor. Quality is the center, but all the other departments and people play a role.”
Training is another big part of their success. Most of the quality employees have taken or are enrolled to take classes through the Technology Manufacturing Association (TMA) of IL. This attention to quality has paid off for the company—and their customers.
“Our customers really tell the story,” says Jim LaCroix, Larsen’s VP of sales and marketing, noting that “customers are very, very happy with what we offer, in terms of responsiveness and metrics. We’ve got sound policies, procedures, work instructions and forms and internal audits in place. When you do what you say and say what you do, it kind of runs itself. With the right level of people and training, it works. This company has a lot of horsepower in terms of quality resources.” LaCroix adds, “When discussing the customer quality side, most of the conversations I’m involved in are short and sweet.”
A History In Manufacturing
The Larsen brothers are fraternal twins who came into the manufacturing field after their grandfather and father. President Dave Larsen and Co-President Denis Larsen come from a long line of manufacturing professionals. Their grandfather Leonard Larsen Sr. began working in manufacturing in the 1940s and their father Leonard Larsen Jr. followed suit. Larsen was founded in 1999, based on this history. In 2001, the company opened the El Paso facility. The company now has 350 employees.
LaCroix says the company has a lot to be proud of. “The fact that it’s grown to what it is, both in revenue scale and amount of offerings, the tools in our tool belt, so to speak, is impressive for a family owned company. We’re corporate minded when we need to be, but we still have that family owned touch,” he says.
While the owners have a long history in manufacturing, they also believe in investing in production equipment and new technology. Among other capital investments, the company recently added a new automated weld line with a robotic arm as well as an automated powder coat paint booth.
Manufacturing today faces a range of issues, including material availability, workforce demands, and supply chain issues, but Larsen has met the challenge. Congratulations to the entire Larsen Manufacturing team on a job well done.
Looking for a reprint of this article?
From high-res PDFs to custom plaques, order your copy today!