Speaking of Quality | Tash Baksh
Incidents, Causal Tools and Effective Corrective Action: Behavior Change for the New Year
How can behavioral changes be made?
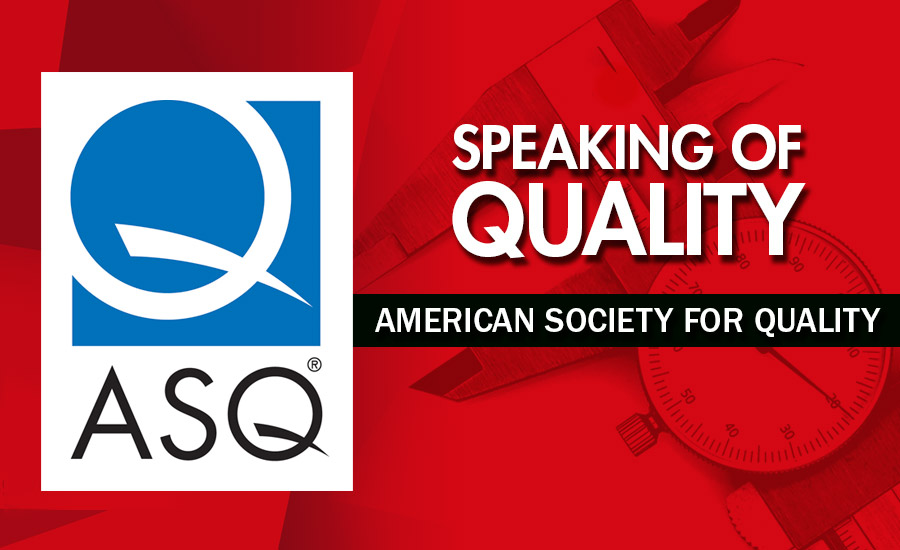
Earlier in my career, I was performing an inspection at height with another worker, when suddenly they slipped and began to fall. As they did, I saw their safety harness engage and rip off to slow their fall almost as if it was in slow motion, then suddenly they grabbed a piece of horizontal rebar and stopped themselves. Ever since that incident I was curious if a true root cause was possible. Was there one cause that triggered an incident?
One of the most enlightening periods in my life was as a young parent when my children would ask me why, followed by another why, and another why, and on and on.
Over the years and many incidents (accidents, injuries, failures, nonconformances) later, I’ve come to recognize that there are many contributing factors to an incident. The key is the corrective action taken. Does the corrective action prevent the incident from recurring? Does it eliminate the risk of the incident and its impact? Conducting a thorough investigation that identifies the several causal factors does help prevent similar incidents from happening again when effective corrective action is taken. By using a causal analysis tool to prevent incidents, we can avoid unnecessary time and pain points we spend reliving past errors that lead to business emergencies and even life interruptions.
Causal Analysis Tools are intended to be used in combination with each other and not exclusively. Below is a list of tools that may be used to conduct causal analysis:
- Brainstorming
- Checklists
- Logic/Event Trees
- Timelines
- Sequence Diagrams
- Causal Factor Determination
For simpler incidents, brainstorming and checklists may be sufficient to identify causal factor determination. For more complicated incidents, logic/event trees should also be considered. Timelines, sequence diagrams, and causal factor identification are often used to support the logic/event tree tool. Regardless of the combination of tools chosen, we should use these tools to answer four important questions:
- What happened?
- How did it happen?
- Why did it happen?
- What corrective action is needed?
How can behavioral changes be made? We need to do something different and have a different outcome. Choices with follow-through action are the main drivers for both continual improvement and personal improvement. This corrective action plan was explained in a past blog of NQA.org, paraphrased as do this and don’t do this. A choice to change behavior and do something different.
The quality practitioner’s goal is to use causal tools to identify the correctable causes, as well as to help create an environment that is likely to attract and retain high-performing staff. Corrective action by itself is not enough for the effective control of incidents; this has to be supported by a leadership system that trusts and respects all members of the team (interested parties).
Creating this inclusive, collaborative place requires each of us to create an environment at work and in our personal lives in which each person feels safe and inspired to share their contributions. A more inclusive environment requires a change in our daily behavior in the areas we control. Learning to embrace differences, listening, empathizing, collaborating, and building trust both professionally and personally is key to effective corrective action. The Barry-Wehmiller company refers to this as being better stewards of people’s lives.
Bibliography:
OSHA Publication available at
https://www.osha.gov/sites/default/files/publications/OSHA3895.pdf
https://www.nqa.com/en-us/resources/blog/october-2016/effective-corrective-action-plan
https://www.barrywehmiller.com/story
Looking for a reprint of this article?
From high-res PDFs to custom plaques, order your copy today!