Tight Pressure Control
Pressure testing is often required to verify that production containers will withstand their rated pressures in the field. Catalina Cylinder (Garden Grove, CA), a producer of high- and low-pressure aluminum cylinders used to transport gases such as oxygen and carbon dioxide, makes its cylinders using a hydraulic forming process. The U.S. Department of Transportation requires that the tanks be pressure tested before being shipped to customers. The testing process involves filling the cylinders with water and then cycling the pressure inside the cylinders for 10,000 cycles while measuring several parameters. The testing cannot exceed 10 cycles per minute, and a certain pressure must be reached during each cycle. Within these constraints, the company has a financial incentive to complete the tests as fast as possible.
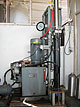
A quicker method of bringing a cylinder up to its rated pressure is to use an intensifier. With an intensifier, pressure from a larger, high-pressure source, such as a reservoir of compressed air, is used to pressurize the cylinder under test. Achieving precise pressure control is still an issue with this method, however, because often the pressurization is done open-loop, meaning that pressure is applied for a period of time without actually measuring the resultant pressure directly each cycle.
Catalina Cylinder had been using the intensifier method when one of its engineers, John Kishel, got an idea for a better way to pressure cycle production cylinders. Kishel had been familiar with electro-hydraulic motion controllers; Catalina Cylinder uses them to operate the cylinder-forming machines. In fact, after Kishel attended a training course at the site of motion controller manufacturer Delta Computer Systems (Vancouver, WA), he got the idea that it may be possible to have a hydraulic actuator, under closed-loop control by one of Delta’s RMC motion controllers, be a source of pressurization for the cylinders under test.

Use of the motion controller gives more precise control and a higher degree of repeatability in the pressure being applied than other techniques. The motion controller is able to control the force being applied to water in the cylinder by monitoring the difference in pressure of hydraulic fluid between the two sides of the piston, and then by moving the piston via a proportional servo valve.
To speed up the process, the Catalina Cylinder test system moves the piston open-loop until pressure is built up inside the production cylinder, and then switches to closed-loop pressure control mode to complete the cycle. Kishel has seen that by using the Delta Computer Systems motion controller, the system can achieve its target pressure to within 1% at 3,000 psi.
One of the other features of the Delta RMC motion controller is that information pertaining to the motion can be interrogated by an external computer and used to document the testing process. In the case of the Catalina Cylinder system, an external programmable logic controller (PLC) accesses information in the Delta controller to keep track of the testing data (peak pressure, cycle rate, number of cycles), which it displays on an operator screen.
An added benefit of using the programmable motion controller and maintaining precise operation is that the test can proceed without close supervision. “You can leave the system running unattended without worrying about having to tweak things,” says Kishel. “The Delta controller combines precision, control and ease of use. There’s no better way to do closed-loop hydraulic control.”
Delta Computer Systems
(360) 254-8688
www.deltacompsys.com
- The motion controller allows Catalina Cylinder to use a PLC to access its testing information for display on an operator screen.
- With the use of the motion controller, testing can proceed unattended.
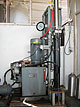
Catalina Cylinder tests high- and low-pressure aluminum cylinders used to transport gases with this apparatus, designed by engineer John Kishel, and incorporating Delta’s motion controllers. Source: Delta Computer Systems
Pressurizing Cylinders
One way of pressure testing cylinders is to fill the cylinders with fluid and then pressurize it using a pump. However, there are problems with this method, including overheating the pump and difficulty achieving precise target pressure. Also, building pressure by pumping can take a lot of time.A quicker method of bringing a cylinder up to its rated pressure is to use an intensifier. With an intensifier, pressure from a larger, high-pressure source, such as a reservoir of compressed air, is used to pressurize the cylinder under test. Achieving precise pressure control is still an issue with this method, however, because often the pressurization is done open-loop, meaning that pressure is applied for a period of time without actually measuring the resultant pressure directly each cycle.
Catalina Cylinder had been using the intensifier method when one of its engineers, John Kishel, got an idea for a better way to pressure cycle production cylinders. Kishel had been familiar with electro-hydraulic motion controllers; Catalina Cylinder uses them to operate the cylinder-forming machines. In fact, after Kishel attended a training course at the site of motion controller manufacturer Delta Computer Systems (Vancouver, WA), he got the idea that it may be possible to have a hydraulic actuator, under closed-loop control by one of Delta’s RMC motion controllers, be a source of pressurization for the cylinders under test.

The motion controller is able to control the force being applied to water in the cylinder by monitoring the difference in pressure of hydraulic fluid between the two sides of the piston, and then by moving the piston via a proportional servo valve. Source: Delta Computer Systems
A Better Way
The system uses a hydraulic cylinder as a pump. The rod end of a hydraulic cylinder goes into a tube that squeezes water into the gas cylinder being tested, according to a motion profile dictated by the program running on the electronic motion controller. High pressures can be achieved quickly, even though the cylinder is moving relatively slowly. And because the hydraulic cylinder moves slowly, the pressurization system has a long life.Use of the motion controller gives more precise control and a higher degree of repeatability in the pressure being applied than other techniques. The motion controller is able to control the force being applied to water in the cylinder by monitoring the difference in pressure of hydraulic fluid between the two sides of the piston, and then by moving the piston via a proportional servo valve.
To speed up the process, the Catalina Cylinder test system moves the piston open-loop until pressure is built up inside the production cylinder, and then switches to closed-loop pressure control mode to complete the cycle. Kishel has seen that by using the Delta Computer Systems motion controller, the system can achieve its target pressure to within 1% at 3,000 psi.
One of the other features of the Delta RMC motion controller is that information pertaining to the motion can be interrogated by an external computer and used to document the testing process. In the case of the Catalina Cylinder system, an external programmable logic controller (PLC) accesses information in the Delta controller to keep track of the testing data (peak pressure, cycle rate, number of cycles), which it displays on an operator screen.
An added benefit of using the programmable motion controller and maintaining precise operation is that the test can proceed without close supervision. “You can leave the system running unattended without worrying about having to tweak things,” says Kishel. “The Delta controller combines precision, control and ease of use. There’s no better way to do closed-loop hydraulic control.”
Delta Computer Systems
(360) 254-8688
www.deltacompsys.com
Benefits
- With the use of a Delta motion controller, Catalina Cylinder’s testing system can achieve its target pressure to within 1% at 3,000 psi.- The motion controller allows Catalina Cylinder to use a PLC to access its testing information for display on an operator screen.
- With the use of the motion controller, testing can proceed unattended.
Looking for a reprint of this article?
From high-res PDFs to custom plaques, order your copy today!